
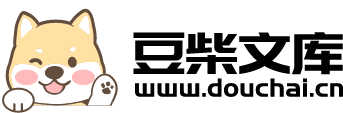
选址与设施布置.pptx
骑着****猪猪
亲,该文档总共33页,到这已经超出免费预览范围,如果喜欢就直接下载吧~
相关资料
设施选址与设施布置.ppt
设施选址与设施布置第一节影响生产与服务设施选址的因素二、设施选址的影响因素二、设施选址的影响因素二、设施选址的影响因素三、不同类型企业的设施选址第二节选址的定量分析方法一、单一设施选址选址程序3.厂址选择的定量分析方法3.厂址选择的方法--分级加权法例1分级加权法3.厂址选择的方法---盈亏平衡法例2:盈亏平衡法3.厂址选择的方法---重心法重心法的解法重心法的解法二、设施网络中的新址选择运输表法例4:运输表法例4:运输表法第3节生产和服务设施(厂区)布置第3节生产和服务设
选址与设施布置.pptx
会计学三、厂址选择方法3.1加权评分法例:某公司业务发展需要,拟建一新厂,现有三个备选厂址供选择,经分析影响因素共有九个,分析结果如下:影响因素3.2重心法/3.3仿真法第二节生产单位配置和专业化形式一、生产单位组成基本生产单位—铸造车间、锻造车间、下料车间、热处理车间、电镀车间、机加工车间、装配车间等。辅助生产单位:工具车间、维修车间、动力车间;生产服务部门:原材料库、半成品库、成品等库、运输队;生产技术准备部门:样品试制车间,工艺技术部门等。二、生产单位的专业化形式1)工艺专业化即把完成相同工艺的设备
设施选址与布置.pptx
会计学23456789101112131415161718192021222324252627282930313233343536373839404142434445464748495051525354555657585960616263646566676869707172737475767778798081828384858687888990919293949596979899100101102103104
生产设施选址与设施布置.pptx
第8章设施选址与设施布置第一节影响生产与服务设施选址的因素二、设施选址的影响因素二、设施选址的影响因素二、设施选址的影响因素三、不同类型企业的设施选址第二节选址的定量分析方法一、单一设施选址选址程序3.厂址选择的定量分析方法3.厂址选择的方法--分级加权法例1分级加权法3.厂址选择的方法---盈亏平衡法例2:盈亏平衡法3.厂址选择的方法---重心法重心法的解法重心法的解法二、设施网络中的新址选择运输表法例4:运输表法例4:运输表法第3节生产和服务设施(厂区)布置第3节生产和服务设施(厂区)布置一、设施布置
生产设施选址与布置.ppt
运营管理选择题模块三设施选址四.设施选址的基本方法四、设施选址定量方法因素评分法举例:一家摄影公司打算开张一家分店,下表是两个可供选择的地点的信息举例:一家摄影公司打算开张一家分店,下表是两个可供选择的地点的信息现欲建造一仓库,有A、B、C三个位置可供选择。建造该配送中心的主要考虑因素有三点,分别是:投资环境、交通便利性、能源供给情况。已知A、B、C三个位置在每项因素上的得分,见表1:同时有4位专家就三种因素给出了各自的权重意见,见表2:重心法步骤一:显示目的地的地图步骤二:加上坐标系步骤三:重心两种情况