
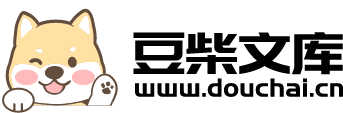
窄流道叶轮的制造方法.pdf
雨巷****可歆
在线预览结束,喜欢就下载吧,查找使用更方便
相关资料
窄流道叶轮的制造方法.pdf
本发明提供窄流道叶轮的制造方法,采用步骤为:S1、面层按照正常工艺制作面层;S2、二层三层按面层在制作两次;S3、三层干燥后,用二层浆料沾浆不浮砂;S4、等到检查干燥后用石英砂堵住流道后倒入硅溶胶;S5、流道干燥后,沾二层浆料和二层砂做过度层;S6、然后根据叶轮的大小加固层两层和三层;S7、封层后脱蜡24小时后即可焙烧;S8、烘焙后浇注;S9、浇注后自然冷却;S10、震壳后叶轮流道里的砂随着震动频率自然流出,因内里是锆砂制壳很容易脱落完成,采用合理的设计思路,通过层与层之间三种元素的相互配合,不添加或者添
窄流道叶轮的制造工艺.docx
窄流道叶轮的制造工艺随着现代工业的发展,叶轮作为液体传动机械的核心部件之一,其在各种工业领域中都有广泛的应用。而窄流道叶轮,作为一种特殊的叶轮类型,其主要是应用在高速、高温、高压等特殊工况下的液体传动系统中。因此,窄流道叶轮的制造工艺也显得至关重要。首先,窄流道叶轮的制造需要选择合适的材料。一般来说,由于窄流道叶轮常受到高温、高压、高速等极端工况的影响,因此需要选择一种高强度、高温、耐腐蚀的特种材料作为基础材料。常见的材料有不锈钢、镍基合金等。由于窄流道叶轮的工作特性,其材料选取必须保证材料的物性及化学性
一种窄流道闭式叶轮制造方法.pdf
本发明公开了一种窄流道闭式叶轮制造方法,将窄流道闭式叶轮设计为分体式的前盖板和开式叶轮体;分别利用铸造模具制作开式叶轮体和前盖板的毛坯,并对铸造完成后的毛坯进行打磨、喷砂处理;然后将加工好的前盖板与开式叶轮体上安装叶片一面对接,且在对接处插入定位销并焊接固定,焊接完成后将该闭式叶轮进行热处理。本发明的制造方法在不影响叶轮强度、轴孔强度的同时,能够保证流道尺寸及表面粗糙度,不存在铸造死角位置打磨清理困难的问题,使得叶轮各流道完全实现设计要求和叶轮性能,使用该方法制造的叶轮能大大提升窄流道闭式叶轮铸造合格率和
一种窄流道离心叶轮的组合焊接方法.pdf
本发明提供了一种窄流道离心叶轮的组合焊接方法,该方法具体包括以下步骤:步骤一,确定角焊段和塞焊段;步骤二,焊前工件准备;步骤三,预热:步骤四,焊接:先对塞焊段进行焊接,然后对角焊段进行焊接;步骤五,焊后消应力:焊接完成后进行进炉消应力处理;步骤六,打磨探伤。本发明的组合焊接方法通过采用角焊+塞焊代替制造成功率低的钎焊。制造过程中的关键为确定角焊和塞焊在整个叶片的比例,确定完比例后,辅助于围带设计,氮气压盖、对中盘工装,增加叶轮支撑,提高焊接质量,更有益于提高叶轮焊接成型成功率,成本低。
一种窄流道叶轮铸件.pdf
本发明涉及一种窄流道叶轮铸件,所述叶轮铸件包括上盖板、下盖板以及位于上盖板和下盖板之间的多个窄流道,所述窄流道的宽度和高度均由内向外平缓递减,所述叶轮铸件的上盖板上位于每个窄流道上方中央的位置开设有带一个台阶的小孔,所述小孔呈方形。本发明结构简单,且能有效提高叶轮质量,减少产品的报废率,降低成本。