
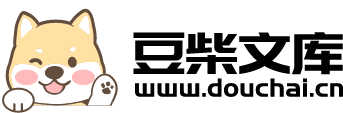
模具表面处理.doc
sy****28
在线预览结束,喜欢就下载吧,查找使用更方便
相关资料
模具表面处理.doc
通过对模具进行表面处理特别是对模具凸、凹模进行表面超硬化处理是解决工件表面拉伤问题经济而有效有方法。表面处理方法有多种,比较常用的有:镀层方面有镀硬铬、化学镀镍磷、刷镀特种、合金等;化学热处理方面有各类渗氮、渗硼、渗硫等;表面超硬化处理方面有化学气相沉积(CVD)物理化学气沉积(PVD)、TD覆层处理。电镀、化学镀、刷镀是通过电化学或化学反应的方法,在工件表面形成合金镀层,工艺不同,合金镀层性能各异。就耐磨抗咬合用途,目前应用较多的是镀硬铬、化学镀镍磷、刷镀镍钨等合金等。对于成形负荷较轻或大型模具采和这些
模具表面处理.ppt
模具表面处理一、前言二、模具表面处理的重要性二、冲压尺寸类型三、模具表面处理分类1.1镀层方面1.2镀硬铬原理1.3镀硬铬工艺路径二、冲压尺寸类型采用金属碳化物扩散覆层TD(ThermalDiffusionCoatingProcess)原理,是在一定的处理温度下将工件置于以硼砂熔盐为载体的特种介质中,通过特种熔盐介质中的金属原子和工件中的碳原子产生化学反应,扩散在工件表面而形成一层几微米至二十余微米的钒、铌、铬、钛、铱、钽等金属碳化层。2.3TD覆层工艺流程二、冲压尺寸类型二、冲压尺寸类型二、冲压尺寸类型
模具表面处理.ppt
模具表面处理一、序言二、模具表面处理的重要性二、冲压尺寸类型三、模具表面处理分类1.1镀层方面1.2镀硬铬原理1.3镀硬铬工艺途径二、冲压尺寸类型采用金属碳化物扩散覆层TD(ThermalDiffusionCoatingProcess)原理,是在一定的处理温度下将工件置于以硼砂熔盐为载体的特种介质中,通过特种熔盐介质中的金属原子和工件中的碳原子产生化学反应,扩散在工件表面而形成一层几微米至二十余微米的钒、铌、铬、钛、铱、钽等金属碳化层。2.3TD覆层工艺流程二、冲压尺寸类型二、冲压尺寸类型二、冲压尺寸类型
模具表面处理.pptx
抛光(Polish)抛光(Polish)SPI-SocietyofthePlasticsIndustry塑料工业协会TypesofFinishes钻石抛光(非常适合镀镍和镀铬)火花纹(ThinFireTexture)号码符号化学蚀纹(Texture)号码Mold-TechAMold-TechCPlaque#6昵宏咬花規格表咬花番號咬花番号咬花番號咬花番號咬花番号咬花番号咬花番号电镀(Plating)非电镀镍Hardness–HVN100氨基磺酸镍电镀电镀硬铬喷砂(Blasting)WetBlasting(
模具表面处理技术.ppt
碳氮共渗的分类四、渗硼渗硼方法渗剂中各部分的作用B4C为硼的来源,KBF4是催渗剂,SiC是填充剂,Mn-Fe则起到使渗剂渗后松散而不结块的作用。一般渗硼后冷至室温开箱时,渗剂松散,工件表面无结垢等现象,无需特殊清理。由于固体渗硼法无需特殊设备,操作简单,工件表面清洁,已逐渐成为最有前途的渗硼方法。2、盐浴渗硼渗硼后的热处理五、渗金属如固体渗铬,渗剂为100~200目铬铁粉(含Cr65%)(40—60)%+NH4Cl(12—3)%,其余为Al2O3,渗铬过程当加热至1050℃的渗铬温度时,氯化铵分解形成H