
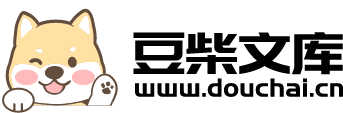
疲劳断口宏观分析.doc
sy****28
在线预览结束,喜欢就下载吧,查找使用更方便
相关资料
疲劳断口宏观分析.doc
1疲劳断口的形貌特征疲劳断口是指金属材料或零构件在疲劳断裂过程中形成的一种匹配的表面,称断裂面或断口。分析它的目的在于确定零构件是否属于疲劳破坏?其破坏的原因是什么?从而提出防止事故的措施和方法,为今后的设计、选材以及加工等问题提出改进意见。对断口的形貌进行分析包括两个方面,即宏观断口分析和微观断口分析。所谓宏观分析是指用肉眼或20—30倍以下放大镜观察断口的形貌特征。微观分析是指用光学显微镜或电子显微镜对断口进行分析。宏观分析不要求专门设备,被观察断口尺寸不受限制,可以观察断件和断口全貌,了解各个方面变
疲劳宏观断口的特征.docx
在日常质量整改过程中,往往会看到一些损坏零件的断口,一些技术人员缺乏“读懂”它的经验,不能从它的断口处判断其断裂原因。本文仅就疲劳断面如何判断作一介绍,希望能对您有所帮助!要点:疲劳宏观断口的特征(见下图)断口拥有三个形貌不同的区域:疲劳源、疲劳区、瞬断区。随材质、应力状态的不同,三个区的大小和位置不同。(表5-1)1、疲劳源裂纹的萌生地;裂纹处在亚稳扩展过程中。由于应力交变,断面摩擦而光亮。加工硬化。随应力状态及应力大小的不同,可有一个或几个疲劳源。2、疲劳区(贝纹区)断面比较光滑,并分布有贝纹线。循环
关于结构钢疲劳断口的宏观分析.docx
关于结构钢疲劳断口的宏观分析标题:结构钢疲劳断口的宏观分析摘要:结构钢的疲劳断口一直以来都是材料科学与工程领域的研究热点之一。本文通过对结构钢疲劳断口的宏观分析,旨在深入了解疲劳断裂行为对结构物的影响,并为结构钢在实际应用中提供理论指导和技术支持。首先,本文将对结构钢的疲劳断裂机理进行综述,并详细介绍宏观分析的关键因素和方法。然后,通过实验数据的分析和模拟仿真,探讨结构钢材料在不同工况下的疲劳断裂特性。最后,总结并展望宏观分析在结构钢疲劳断口研究中的应用前景。关键词:结构钢,疲劳断口,宏观分析,断裂机理,
疲劳断口的宏观形貌特征.ppt
疲劳断口的宏观形貌特征目录疲劳断口的观察方法疲劳断口的观察方法疲劳断口的观察方法疲劳断口的观察方法疲劳断口的宏观形貌特征疲劳断口的宏观形貌特征疲劳断口的宏观形貌特征疲劳断口的宏观形貌特征疲劳断口的宏观形貌特征疲劳断口的宏观形貌特征疲劳断口的宏观形貌特征根据宏观形貌特征判断受载情况根据宏观形貌特征判断受载情况根据宏观形貌特征判断受载情况谢谢!
疲劳断口的宏观形貌特征.ppt
疲劳断口的宏观形貌特征目录疲劳断口的观察方法疲劳断口的观察方法疲劳断口的观察方法疲劳断口的观察方法疲劳断口的宏观形貌特征疲劳断口的宏观形貌特征疲劳断口的宏观形貌特征疲劳断口的宏观形貌特征疲劳断口的宏观形貌特征疲劳断口的宏观形貌特征疲劳断口的宏观形貌特征根据宏观形貌特征判断受载情况根据宏观形貌特征判断受载情况根据宏观形貌特征判断受载情况谢谢!