
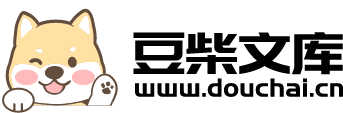
钢的表面热处理.ppt
mm****酱吖
亲,该文档总共27页,到这已经超出免费预览范围,如果喜欢就直接下载吧~
相关资料
钢的热处理及表面热处理.docx
第PAGE\*Arabic\*MERGEFORMAT14页共NUMPAGES\*MERGEFORMAT14页钢的热处理及表面热处理钢的热处理及表面热处理热处理1.定义。指将材料在固态下加热到一定温度,保温一定时间,以适当速度冷却,以获得所需组织结构和性能的工艺方法。2.热处理的工艺过程。包括三个阶段:加热、保温和冷却,如图所示。加热:热处理的第一道工序。不同的材料,其加热工艺和加热温度都不同。保温。目的是要保证工件烧透,防止脱碳、氧化等。保温时间和介质的选择与工件的尺寸和材质有直接的关系。一般
钢的热处理及表面热处理.docx
第PAGE\*Arabic\*MERGEFORMAT14页共NUMPAGES\*MERGEFORMAT14页钢的热处理及表面热处理钢的热处理及表面热处理热处理1.定义。指将材料在固态下加热到一定温度,保温一定时间,以适当速度冷却,以获得所需组织结构和性能的工艺方法。2.热处理的工艺过程。包括三个阶段:加热、保温和冷却,如图所示。加热:热处理的第一道工序。不同的材料,其加热工艺和加热温度都不同。保温。目的是要保证工件烧透,防止脱碳、氧化等。保温时间和介质的选择与工件的尺寸和材质有直接的关系。一般
钢的热处理及表面热处理.docx
钢的热处理及表面热处理钢的热处理及表面热处理热处理1.定义。指将材料在固态下加热到一定温度保温一定时间以适当速度冷却以获得所需组织结构和性能的工艺方法。2.热处理的工艺过程。包括三个阶段:加热、保温和冷却如图所示。加热:热处理的第一道工序。不同的材料其加热工艺和加热温度都不同。保温。目的是要保证工件烧透防止脱碳、氧化等。保温时间和介质的选择与工件的尺寸和材质有直接的关系。一般按每分种1~2毫米计算;工件越大材料的导热性越差保温时间就越长。
钢的热处理及表面热处理.docx
第PAGE\*Arabic\*MERGEFORMAT14页共NUMPAGES\*MERGEFORMAT14页钢的热处理及表面热处理钢的热处理及表面热处理热处理1.定义。指将材料在固态下加热到一定温度,保温一定时间,以适当速度冷却,以获得所需组织结构和性能的工艺方法。2.热处理的工艺过程。包括三个阶段:加热、保温和冷却,如图所示。加热:热处理的第一道工序。不同的材料,其加热工艺和加热温度都不同。保温。目的是要保证工件烧透,防止脱碳、氧化等。保温时间和介质的选择与工件的尺寸和材质有直接的关系。一般
钢的表面热处理.ppt
钢的表面热处理表面淬火:仅对工件表层进行淬火的热处理工艺。原理:通过快速加热,使钢的表层奥氏体化,在热量尚未充分传到零件中心时就立即予以冷却淬火,得到马氏体组织。目的:使工件表面获得高硬度和高耐磨性,而心部保持较好的塑性和韧性,以提高其在扭转、弯曲、循环应力或在摩擦、冲击、接触应力等工作条件下的使用寿命。适用:中碳钢、中碳合金钢。方法:火焰加热表面淬火、感应加热表面淬、电接触加热表面淬火、激光加热表面淬火。(1)感应加热表面淬火1)感应加热基本原理利用感应电流通过工件所产生的热效应,使工件表面受到局部加热