
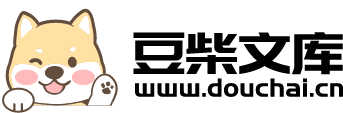
轴流导叶式气液旋流分离器的试验研究(完整版)实用资料.doc
天马****23
亲,该文档总共97页,到这已经超出免费预览范围,如果喜欢就直接下载吧~
相关资料
轴流导叶式气液旋流分离器的试验研究(完整版)实用资料.doc
轴流导叶式气液旋流分离器的试验研究(完整版)实用资料(可以直接使用,可编辑完整版实用资料,欢迎下载)轴流导叶式气液旋流分离器的试验研究金向红3金有海王振波(中国石油大学摘要轴流导叶式气液旋流分离器与其他离心式气液分离器比较,其特点是阻力损失小。经试验证明,在低含液浓度下该分离器对气液两相具有较高的分离效果,且采用合理的溢流管和筒体结构形式可以减少短路流和二次流夹带,提高其分离效率。关键词旋流器气液分离导向叶片分离效率压降损失中图分类号TQ05118+4文献标识码A文章编号025426094(2007022
轴流式气液旋流分离器的试验研究与数值模拟.docx
轴流式气液旋流分离器的试验研究与数值模拟轴流式气液旋流分离器的试验研究与数值模拟摘要随着工业技术的不断发展,气液旋流分离器作为一种重要的分离设备,广泛应用于化工、石油、能源等领域。本文通过试验研究和数值模拟的方法,对轴流式气液旋流分离器进行了研究。试验研究利用实验装置进行了气液旋流分离的性能测试,数值模拟使用计算流体动力学方法对分离器的流动特性进行了模拟。研究结果表明,轴流式气液旋流分离器具有良好的分离效果,并且数值模拟结果与试验结果吻合较好。本文为轴流式气液旋流分离器的应用提供了理论依据和技术支持。关键
轴流式双筒体气液旋流分离器性能试验研究.docx
轴流式双筒体气液旋流分离器性能试验研究摘要本研究对轴流式双筒体气液旋流分离器的性能进行了试验研究。试验结果表明,该旋流分离器能有效地分离气液混合物,具有较高的分离效率和压降小的特点。同时,在不同入口气液速度、双筒体间距、旋流器结构参数等因素的影响下,分离器表现出不同的工作性能。因此,在实际应用中应根据工况和分离要求来选择最优的工作参数,以获得最佳的分离效果。关键词:气液旋流分离器,性能试验,分离效率,压降引言在石油、化工、环保等领域中,气液分离是非常重要的过程。传统的气液分离方式包括重力分离、离心分离、过
轴流导叶式旋流分离器的数值模拟与实验性能研究.docx
轴流导叶式旋流分离器的数值模拟与实验性能研究轴流导叶式旋流分离器的数值模拟与实验性能研究摘要:轴流导叶式旋流分离器是一种常用的分离设备,广泛应用于化工、环保和液固分离等领域。本论文通过数值模拟和实验研究,对轴流导叶式旋流分离器的性能进行了探究。首先,使用计算流体力学方法建立了数值模型,对轴流导叶式旋流分离器内流场进行了仿真。然后,设计并搭建了实验装置,通过实验测量了轴流导叶式旋流分离器的分离效果和压降特性。最后,对比分析了数值模拟结果和实验数据,探讨了轴流导叶式旋流分离器的优缺点和改进方向。关键词:轴流导
轴流导叶式旋风分离器气液分离特性的优化研究的开题报告.docx
轴流导叶式旋风分离器气液分离特性的优化研究的开题报告1.研究背景及意义随着生产和工业的不断发展,气液分离技术在工业领域、环保领域和能源领域中得到了广泛的应用。旋风分离器是一种常见的气液分离设备,其依靠离心力将气体和固体或液体分离。然而,由于旋风分离器存在分离效率低、压降大、能耗高等问题,因此分离效率和经济性的提高一直是研究者们关注的焦点。为提高旋风分离器的分离效率和经济性,本文将针对轴流导叶式旋风分离器展开优化研究,以提高其气液分离特性。2.研究内容及方法研究内容:(1)轴流导叶式旋风分离器气液分离特性分