
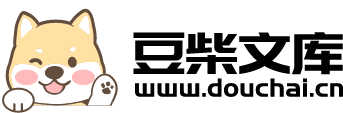
飞秒激光微加工技术研究进展.pdf
yy****24
在线预览结束,喜欢就下载吧,查找使用更方便
相关资料
飞秒激光微加工技术研究进展.pdf
飞秒激光微加工技术研究进展黄文浩中国科学技术大学精密机械与精密仪器系合肥230026摘要:本文主要介绍近两年来飞秒激光微加工技术进展,其中包括飞秒激光微加工原理与实验系统,微加工工艺研究以及双光子飞秒激光三维微器件和三维信息存储研究。对双光子飞秒激光加工点分辨率也进行了有益的探索。我们在国家自然科学基金和863,985工程的资助下对飞秒双光子加工装备和加工工艺进行了深入研究,现将取得的阶段性结果报告如下:1.飞秒双光子三维微细加工实验系统从功能上划分,现有加工系统由以下四个部分组成:1)飞秒激发源。它由泵
飞秒激光微加工技术研究进展.pdf
飞秒激光微加工技术研究进展黄文浩中国科学技术大学精密机械与精密仪器系合肥230026摘要:本文主要介绍近两年来飞秒激光微加工技术进展,其中包括飞秒激光微加工原理与实验系统,微加工工艺研究以及双光子飞秒激光三维微器件和三维信息存储研究。对双光子飞秒激光加工点分辨率也进行了有益的探索。我们在国家自然科学基金和863,985工程的资助下对飞秒双光子加工装备和加工工艺进行了深入研究,现将取得的阶段性结果报告如下:1.飞秒双光子三维微细加工实验系统从功能上划分,现有加工系统由以下四个部分组成:1)飞秒激发源。它由泵
飞秒激光微加工技术在微加工中的应用.doc
飞秒激光微加工技术在微加工中的应用1飞秒激光加工微结构基于能量高度集中、热影响区小、无飞溅无熔渣、不需特殊的气体环境、无后续工艺、双光子聚合加工精度可达0.7μm等优势,飞秒激光在诱导金属微结构加工应用方面和精细加工方面都取得了很大的进展。(1)孔加工在1mm厚的不锈钢薄片上,飞秒激光进行了具有深孔边缘清晰、表面干净等特点的纳米级深孔加工(如图1a);在金属薄膜上,钛宝石飞秒激光加工制备出了微纳米级阵列孔(如图1b),孔径最小达2.5μm,孔直径在2.5~10μm间可调,最小间距可达10μm,很容易实现1
飞秒激光微加工技术的评述与展望.docx
飞秒激光微加工技术的评述与展望随着现代科学技术的不断发展,人们对微加工技术的需求越来越高。并且,随着微纳米结构的应用越来越广泛,对实现高精度、高质量微加工技术的要求也越来越高。飞秒激光微加工技术作为一种新型微加工技术,以其高效、高精度、高质量的特点受到了广泛关注。本文将从技术原理、应用现状以及未来发展等方面对飞秒激光微加工技术进行评述和展望。一、技术原理飞秒激光微加工技术的原理是使用飞秒激光对材料进行加工,通过光子直接击穿材料表面形成微小孔洞。由于飞秒激光对于材料的加工瞬间非常快,因此会产生非热平衡等离子
飞秒激光微加工技术的评述与展望.pdf
飞秒激光微加工技术的评述与展望黄佑香,张庆茂,廖健宏,周永恒(华南师范大学激光加工实验室,广东广州510006)摘要:综述了飞秒激光微加工技术国内外的研究现状,介绍了飞秒激光微加工在光学、微电子及生物医学等领域的应用,展望了飞秒激光微加工技术未来发展的趋势以及需要解决的关键技术。关键词:飞秒激光;应用;微加工;进展中图分类号:TN249;TG665文献标识码:A文章编号:025426051(2008)0620008206Reviewandprospectsoffemtosecondlasermicro2p