
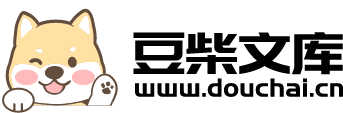
燕尾槽《燕尾槽的铸造工艺设计》12000字.doc
一吃****春艳
亲,该文档总共27页,到这已经超出免费预览范围,如果喜欢就直接下载吧~
相关资料
燕尾槽《燕尾槽的铸造工艺设计》12000字.doc
燕尾槽的铸造工艺设计摘要劈挤是一种新近命名的尚处于研究和探索阶段的局部连续塑性成形方法。本文以槽深为10mm、槽底宽为12mm的燕尾槽作为研究对象,借助数值模拟和物理模拟方法,研究了燕尾槽劈楔劈挤变形过程,初步归纳了其成形规律。论文的主要工作以及取得的成果有如下几个方面:(1)提出了燕尾槽劈挤成形的研究方案,确定了以劈分角(a)、劈入角(β)、.燕尾角(0)为劈挤主要影响因素以及主要成形指标稳态变形时的最大成形加(P)、槽侧隆起高度(H)和隆起影响宽度(B)、劈入塌角(A)、不稳定隆起长度(L)以及废料相
燕尾槽《燕尾槽的铸造工艺设计》12000字.doc
燕尾槽的铸造工艺设计摘要劈挤是一种新近命名的尚处于研究和探索阶段的局部连续塑性成形方法。本文以槽深为10mm、槽底宽为12mm的燕尾槽作为研究对象,借助数值模拟和物理模拟方法,研究了燕尾槽劈楔劈挤变形过程,初步归纳了其成形规律。论文的主要工作以及取得的成果有如下几个方面:(1)提出了燕尾槽劈挤成形的研究方案,确定了以劈分角(a)、劈入角(β)、.燕尾角(0)为劈挤主要影响因素以及主要成形指标稳态变形时的最大成形加(P)、槽侧隆起高度(H)和隆起影响宽度(B)、劈入塌角(A)、不稳定隆起长度(L)以及废料相
燕尾槽《燕尾槽的铸造工艺设计》开题报告.doc
开题报告学生姓名院(系)部专业班级题目《燕尾槽的铸造工艺设计》选题背景、目的及意义劈挤是一种新近命名的尚处于研究和探索阶段的局部连续塑性成形方法。本文以槽深为10mm、槽底宽为12mm的燕尾槽作为研究对象,借助数值模拟和物理模拟方法,研究了燕尾槽劈楔劈挤变形过程,初步归纳了其成形规律。论文的主要工作以及取得的成果有如下几个方面:(1)提出了燕尾槽劈挤成形的研究方案,确定了以劈分角(a)、劈入角(β)、.燕尾角(0)为劈挤主要影响因素以及主要成形指标稳态变形时的最大成形加(P)、槽侧隆起高度(H)和隆起影响
燕尾槽《燕尾槽的铸造工艺设计》12000字.doc
燕尾槽的铸造工艺设计摘要劈挤是一种新近命名的尚处于研究和探索阶段的局部连续塑性成形方法。本文以槽深为10mm、槽底宽为12mm的燕尾槽作为研究对象,借助数值模拟和物理模拟方法,研究了燕尾槽劈楔劈挤变形过程,初步归纳了其成形规律。论文的主要工作以及取得的成果有如下几个方面:(1)提出了燕尾槽劈挤成形的研究方案,确定了以劈分角(a)、劈入角(β)、.燕尾角(0)为劈挤主要影响因素以及主要成形指标稳态变形时的最大成形加(P)、槽侧隆起高度(H)和隆起影响宽度(B)、劈入塌角(A)、不稳定隆起长度(L)以及废料相
燕尾槽《燕尾槽的铸造工艺设计》开题报告.doc
开题报告学生姓名院(系)部专业班级题目《燕尾槽的铸造工艺设计》选题背景、目的及意义劈挤是一种新近命名的尚处于研究和探索阶段的局部连续塑性成形方法。本文以槽深为10mm、槽底宽为12mm的燕尾槽作为研究对象,借助数值模拟和物理模拟方法,研究了燕尾槽劈楔劈挤变形过程,初步归纳了其成形规律。论文的主要工作以及取得的成果有如下几个方面:(1)提出了燕尾槽劈挤成形的研究方案,确定了以劈分角(a)、劈入角(β)、.燕尾角(0)为劈挤主要影响因素以及主要成形指标稳态变形时的最大成形加(P)、槽侧隆起高度(H)和隆起影响