
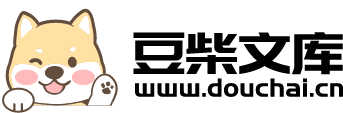
车身结构轻量化优化方法.pdf
猫巷****晓容
在线预览结束,喜欢就下载吧,查找使用更方便
相关资料
车身结构轻量化优化方法.pdf
本发明公开了一种车身结构轻量化优化方法,包括以下步骤:步骤A、轻量化目标制定;步骤B、车身拓扑优化;步骤C.车身结构形貌优化;步骤D.车身尺寸和形状优化;步骤E.车身性能验证。本发明在概念设计阶段,通过全局拓扑和局部拓扑方法分析每一种载荷工况的传递路径和主要承载结构,从而获得主要承力部件最合理的布置位置。在详细设计阶段,对于零件最合理的厚度尺寸、梁结构最合理的截面形状及钣金件最合理的加强筋布置方案,分别采用尺寸优化和形貌优化方法来实现。本发明使设计车身在满足性能要求的前提下,能够极大提升了材料利用率和产品
一种车身结构轻量化优化方法.pdf
本发明涉及一种车身结构轻量化优化方法,所述的方法包括建立车身结构参数化有限元模型;利用相关性分析方法分析预先给定的60个位置、形状及厚度等设计变量对车身结构刚度的影响,筛选出有轻量化潜力的设计变量;根据结构性能参数相对形状变量的变化梯度即为灵敏度的大小对形状变量进行筛选,所述的对筛选出来的30个设计变量进行多性能优化设计;以经筛选后的形状等变量为优化变量,并设置约束条件,以车身轻量化和结构性能最优为目标,以得到较好的轻量化效果。本发明通过建立车身结构有限元模型,根据结构性能参数相对形状变量的变化梯度对形状
车身结构分析及轻量化优化设计.pdf
江苏大学硕士学位论文车身结构分析及轻量化优化设计姓名:孙军申请学位级别:硕士专业:车辆工程指导教师:朱茂桃;陈上华20040601摘要关键词:车身,有限元,强度,设计优化,拓扑形状优化汽车车身轻量化技术是一项关键技术,本文运用有限元方法和试验相结合的手段研究了改型后某军车的结构性能。通过有限元计算得到了该车在满载弯曲、扭转等工况下的结构强度和刚度特性,并对各种工况下车身及车架关键部位的应力、变形的分布进行了分析。同时采用传统的电测量方法测量了车型样车在相应工况下的强度和刚度状况,并与计算值相比较,检验了该
基于多目标稳健性优化方法的SUV车身结构轻量化设计简.ppt
基于多目标稳健性优化方法的SUV车身结构轻量化设计汽车工程领域三大主题课题研究现状及课题提出汽车侧面碰撞流程自动化系统的开发汽车侧面碰撞流程自动化系统的开发汽车侧面碰撞流程自动化系统的开发汽车侧面碰撞流程自动化系统的开发汽车侧面碰撞流程自动化系统的开发SUV有限元模型的建立与有限元分析汽车侧面碰撞流程自动化系统的开发汽车侧面碰撞流程自动化系统的开发SUV有限元模型的建立与有限元分析SUV有限元模型的建立与有限元分析SUV有限元模型的建立与有限元分析SUV有限元模型的建立与有限元分析SUV有限元模型的建立与
车身结构优化方法及系统.pdf
本发明公开了一种车身结构优化方法及系统,所述方法包括:获取车身的悬架物理结构,并根据该悬架物理结构搭建多体动力学模型;通过多体动力学仿真软件分析车轮随悬架跳动时的运动状况,并根据悬架零件敏感度对车轮运动状况进行调整;对悬架主要衬套特性进行调整,使衬套吸收更多来自车轮的冲击能量。该方法在设计阶段便能通过多体运动学分析确认悬架机构的运动特性,根据车辆参数信息重新优化设计衬套结构,在进行底盘开发过程中能够极大程度的借用已有的悬架结构,提升零件的通用性,有效降低底盘开发和优化成本,且能够极大提升车辆的性能。