
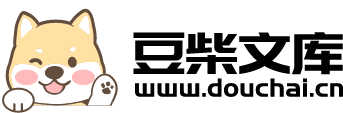
薄壁复杂铝合金铸件低压铸造工艺实践.pdf
yy****24
在线预览结束,喜欢就下载吧,查找使用更方便
相关资料
薄壁复杂铝合金铸件低压铸造工艺实践.pdf
薄壁复杂铝合金铸件低压铸造工艺实践-郭忠民陈大胜(西安黄河机电有限公司,陕西西安710043)摘要:根据低压铸造工艺的特点和生产实践,从补缩、内浇道设计、排气、信号线安放位置等方面进行了分析和探讨。针对铸件的不对称结构提出了充型过程中铝液的分配问题,引入结构质量分数的概念。由生产实践总结出信号线的安放位置不一定在型腔最高点,而应在金属液最后充填的位置。关键词:低压铸造;薄壁复杂件;铝液分配;结构质量分数;信号线铸件在形成过程中必须控制充型与凝固两个限制,往往难以实现所期望的顺序凝固,同时由于充过程,它们在
薄壁铝合金铸件低压铸造的数值模拟与工艺优化.docx
薄壁铝合金铸件低压铸造的数值模拟与工艺优化薄壁铝合金铸件低压铸造的数值模拟与工艺优化一、引言近年来,随着航空、汽车、船舶、电力等行业的不断发展,对于轻量化、节能、环保等方面的要求也越来越高。因此,铝合金在这些行业中得到了广泛的应用。在铝合金制品中,薄壁铸件具有高强度、优良的导热性、良好的耐腐蚀性等优点,因此广泛应用于各种领域。低压铸造是一种被广泛应用于铝合金铸造中的现代化技术,它具有工艺性好、工件质量稳定、成本低廉等优点。在铝合金薄壁铸件低压铸造中,通过数值模拟对其生产工艺进行优化,可以有效地提高铸件的质
复杂箱体铸件低压铸造工艺改进.docx
复杂箱体铸件低压铸造工艺改进随着制造技术和工艺的不断进步,复杂箱体铸造件在工业制造领域中被广泛应用,因其具有高强度、耐热、耐磨、耐腐蚀、密封性好等特点,并广泛应用于汽车、军工、航空航天和船舶等领域。低压铸造是目前生产复杂箱体铸件的主要方法之一,通过改进低压铸造工艺,可以提高箱体铸造件的生产效率和质量,本文将探讨复杂箱体铸件低压铸造工艺改进的方法与应用。一、复杂箱体铸件低压铸造的优势低压铸造是一种半自动化铸造方法,具有生产效率高,产品质量稳定等优点,其主要优势如下:1.精度高:由于低压铸造的熔体在压力的作用
复杂薄壁铝合金铸件磁动力真空调压铸造工艺研究.docx
复杂薄壁铝合金铸件磁动力真空调压铸造工艺研究引言铝合金材料在工业制造中广泛应用。其中,薄壁铝合金铸件作为一种轻质高强度材料,已成为高端汽车、航空航天等领域的首选材料。而在制造薄壁铝合金铸件时,通常采用真空压铸工艺,以获得更高的尺寸精度和表面质量。然而,由于铝合金材料的高热传导性和低熔点,使得在真空压铸过程中难以获得理想的制品性能。因此,对于薄壁铝合金铸件的制造过程进行研究是非常有必要的。本篇论文介绍了一种新的工艺——磁动力真空调压铸造(MHDVC)工艺,它通过磁场控制和真空封闭的方式,有效解决了铝合金材料
ZM4镁合金复杂薄壁壳体铸件低压铸造工艺研究.docx
ZM4镁合金复杂薄壁壳体铸件低压铸造工艺研究摘要本文主要研究了ZM4镁合金复杂薄壁壳体铸件的低压铸造工艺。首先介绍了镁合金的优点和应用,然后阐述了低压铸造的基本原理和特点。接着详细介绍了研究过程中的试验方法和测试结果,通过对试验数据的分析和对比,得出了最优工艺参数的选择,并对最终制备出的样件进行了性能测试,展示了该工艺方法的可行性和实用性。最后,对本文研究工作进行了总结和展望。关键词:ZM4镁合金;复杂薄壁壳体铸件;低压铸造;工艺研究简介镁合金作为一种重要的轻质高强材料,在汽车、航空航天、电子、医疗器械等