
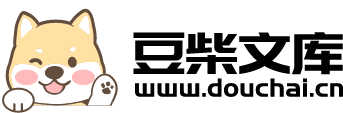
刍议线切割加工模具的工艺要点.docx
努力****梓颖
在线预览结束,喜欢就下载吧,查找使用更方便
相关资料
刍议线切割加工模具的工艺要点.docx
刍议线切割加工模具的工艺要点1引言线切割是冲模零件的主要加工方式然而进行合理的工艺分析正确计算数控编程中电极丝的设计走丝轨迹关系到模具的加工精度。通过穿丝孔的确定与切割路线的优化改善切割工艺这对于提高切割质量和生产效率是一条行之有效的重要途径。2实际轨迹的计算根据大量的统计数据表明线切割加工后的实际尺寸大部分处于公差带的中位值(或称“中间尺寸”)附近因此对于冲模零件图样中标注公差的尺寸应采用中位值尺寸作为实际切割轨迹的编程数据其计算公式为:中
刍议线切割加工模具的工艺要点.docx
刍议线切割加工模具的工艺要点1引言线切割是冲模零件的主要加工方式然而进行合理的工艺分析正确计算数控编程中电极丝的设计走丝轨迹关系到模具的加工精度。通过穿丝孔的确定与切割路线的优化改善切割工艺这对于提高切割质量和生产效率是一条行之有效的重要途径。2实际轨迹的计算根据大量的统计数据表明线切割加工后的实际尺寸大部分处于公差带的中位值(或称“中间尺寸”)附近因此对于冲模零件图样中标注公差的尺寸应采用中位值尺寸作为实际切割轨迹的编程数据其计算公式为:中
刍议线切割加工模具的工艺要点.docx
刍议线切割加工模具的工艺要点1引言线切割是冲模零件的主要加工方式然而进行合理的工艺分析正确计算数控编程中电极丝的设计走丝轨迹关系到模具的加工精度。通过穿丝孔的确定与切割路线的优化改善切割工艺这对于提高切割质量和生产效率是一条行之有效的重要途径。2实际轨迹的计算根据大量的统计数据表明线切割加工后的实际尺寸大部分处于公差带的中位值(或称“中间尺寸”)附近因此对于冲模零件图样中标注公差的尺寸应采用中位值尺寸作为实际切割轨迹的编程数据其计算公式为:中
线切割加工模具工艺基准.docx
线切割加工模具工艺基准线切割加工模具工艺基准摘要:线切割加工技术是一种高精度、高效率的金属加工技术,广泛应用于模具制造行业。本论文将基于线切割加工技术,探讨模具工艺基准的重要性以及线切割加工模具的工艺基准。关键词:线切割加工,模具工艺,基准1.引言模具制造是现代制造业的重要组成部分,其在汽车、电子、航空等领域中广泛应用。模具的精密度和质量直接影响到制造工艺的稳定性和产品的质量。线切割加工技术由于其高精度、高效率的特点,成为模具制造中不可或缺的工艺之一。而模具工艺基准则是确保线切割加工模具质量和精度的重要保
模具线切割加工.doc
本节要点线切割原理线切割特点线切割机床数字控制原理教学目标:掌握线切割加工的原理和特点;了解电火花线切割机床的组成;了解数字程序控制的基本原理。一、线切割加工原理和特点1、电火花线切割加工的基本原理与电火花成型加工一样,也是利用工具电极对工件进行脉冲放电时产生的电腐蚀现象来进行加工的。但是,电火花线切割加工不需要制作成型电极,而是用运动着的金属丝(钼丝或铜丝)作电极,利用电极丝和工件在水平面内的相对运动切割出各种形状的工件。若使电极丝相对工件进行有规律的倾斜运动,还可以切割出带锥度的工件。工件接在脉冲电源