
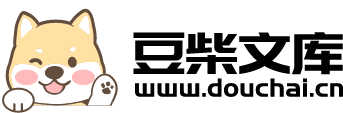
自冲铆接头组织及性能分析.pdf
qw****27
在线预览结束,喜欢就下载吧,查找使用更方便
相关资料
自冲铆接头组织及性能分析.pdf
第35卷第7期焊接学报Vol.35No.72014年7月TRANSACTIONSOFTHECHINAWELDINGINSTITUTIONJuly2014自冲铆接头组织及性能分析许竞楠,何晓聪,曾凯,邢宝英(昆明理工大学机电工程学院,昆明650500)摘要:分析了有铆自冲铆接和压印连接的工艺特点,对比了两种不同连接方式的接头抗拉伸-抗剪强度;利用阳极化覆膜的方法制备接头金相试样,对接头机械自锁区材料的组织及流向进行观测.结果表明,有铆自冲铆接的抗拉伸-抗剪强度高于压印连接.机械连接导致的材料塑性变形,使晶粒
自冲铆成形机理及静力学性能分析.docx
自冲铆成形机理及静力学性能分析自冲铆成形技术是一种新型的金属连接技术,具有质量轻、可重复使用、高效率、无需处理、节能环保等优点,因此在航空航天、汽车、机械制造和建筑等领域得到了广泛应用。本文旨在探讨自冲铆成形的机理及其静力学性能分析。自冲铆成形机理自冲铆成形是利用搭接材料之间的弹性变形,使铆钉箍住了板材,从而完成了铆接的过程。具体的成形过程可以分为三个阶段:柄部加锈、锥形攻入和成形锁紧。以下是详细的描述:1.柄部加锈:自冲铆需要使用特制的铆钉,铆钉有一定的锋利度,采用异步进给的方式,通过搭接材料以及对材料
自冲铆成形机理及静力学性能分析.docx
自冲铆成形机理及静力学性能分析Title:AnalysisofSelf-PierceRiveting:MechanismsandStaticMechanicalPropertiesIntroduction:Self-pierceriveting(SPR)isawidelyusedjoiningprocessinvariousindustries,includingautomotive,aerospace,andmaritimeindustries.Itinvolvesjoiningtwoormoremat
TA1钛合金板异质粘接-自冲铆复合接头力学性能研究.docx
TA1钛合金板异质粘接-自冲铆复合接头力学性能研究TA1钛合金板异质粘接-自冲铆复合接头力学性能研究摘要:TA1钛合金在航空、航天等领域具有重要的应用价值。为了提高TA1钛合金板材的力学性能,实现异质粘接-自冲铆复合接头具有重要意义。本文通过分析TA1钛合金板异质粘接-自冲铆复合接头的力学性能,探讨了其应力分布、刚度和接头强度等方面的变化规律,为TA1钛合金板的应用研究提供了理论依据。关键词:TA1钛合金板,异质粘接,自冲铆,力学性能,应力分布1.引言TA1钛合金是一种重要的结构材料,具有优异的耐腐蚀性和
自冲铆连接结构以及冲铆钉.pdf
本发明涉及一种自冲铆连接结构,其具有至少两个由强度最高为300MPa的能变形的金属材料、尤其是铝质材料制成的构件(1、3),所述构件在一个铆接过程中相互连接,在其中,冲铆钉(5)以设定力(F)穿过凸模侧的第一构件(1)并且钉入凹模侧的第二构件(3)中,确切的说,在第二构件(3)中保留剩余底部厚度(r)的情况下并且在冲铆钉(5)在第二构件(3)中扩张到的扩张直径(d