
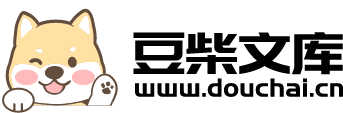
深孔钻削加工方法和深孔钻削用刀柄.pdf
努力****采萍
亲,该文档总共11页,到这已经超出免费预览范围,如果喜欢就直接下载吧~
相关资料
深孔钻削加工方法和深孔钻削用刀柄.pdf
本发明涉及机械钻孔技术领域,公开一种深孔钻削加工方法和深孔钻削用刀柄,钻头被刀柄带动旋转加工工件,设置曲线路径,使刀柄绕曲线路径运转,带动钻头与工件发生间歇性接触,所述曲线路径为规律的波浪线,所述波浪线的波峰波谷对称,波峰和波谷的朝向与刀柄轴向平行。本加工方法创新地设计供刀柄在旋转过程中依路径运转的曲线路径,刀柄带动钻头在刀柄轴向产生周期往复运动,使钻头与工件发生周期性接触和不接触,进而产生碎小切屑,达到理想的断屑和顺畅排屑效果,有效延长钻头的使用寿命,同时解决了传统深孔加工中排屑困难、钻头冷却不充分、深
深孔钻削方法、用于深孔钻削机的工具、深孔钻削机和离心铸管.pdf
本发明涉及一种用于制造具有内轮廓的管(104)的深孔钻削方法,该内轮廓具有沿管(104)的内侧螺旋地延伸的至少一个凹部,其中利用深孔钻削机(100),使包括沿纵向轴线延伸的基体和布置在基体外圆周上的至少一个切削刃的工具(1)被拉动或推动通过管(104)的内部,同时使其围绕其纵向轴线转动,使得切削刃沿管(104)的内侧的螺旋切割线完成切割。
深孔钻削工艺及深孔钻床.docx
深孔钻削工艺及深孔钻床深孔钻削工艺及深孔钻床摘要:深孔钻削工艺是一种用于钻削深孔的专门工艺。随着工业对深孔加工要求的提高,深孔钻削工艺得到了越来越多的关注和应用。本文将介绍深孔钻削工艺的原理和特点,并介绍常用的深孔钻床的分类及其特点。关键词:深孔钻削,工艺,钻床一、引言随着工业技术的发展和生产要求的提高,对于产品中深孔的加工要求也越来越高。深孔加工是指在工件中钻削深孔,通常是用于生产特定零件或应用特定工艺。深孔钻削工艺是深孔加工中最常用也是最重要的工艺之一。深孔钻削工艺的发展得益于钻削技术、微加工技术以及
深孔钻削的探讨.docx
深孔钻削的探讨深孔钻削的探讨引言:深孔钻削是一种特殊的加工过程,广泛应用于航空航天、汽车、军工等高精度、高耐磨的领域。深孔钻削具有加工效率高、质量稳定、成本低等优点,因此备受关注。本论文将探讨深孔钻削的原理、工艺优化和发展趋势。一、深孔钻削原理1.1切削力的分析深孔钻削过程中,切削力是影响加工质量和加工效率的关键因素之一。切削力大小与切削速度、进给量、切削合金、切削液等因素有关。研究切削力的分布规律可以帮助我们更好地理解深孔钻削过程。1.2热变形及应力分析由于深孔钻削中切削过程中会产生大量的热量,而热量会
深孔钻削应用指南.docx
深孔钻削应用指南深孔钻削可采用多种机床安装方式:工件旋转,刀具做进给运动;工件不动,刀具旋转又做进给运动;工件旋转,刀具做反向旋转又做进给运动。具体采用何种方式则依据工件特征及所加工孔的情况而定。目前常用的深孔钻削加工系统有枪钻系统、BTA单管钻系统、喷吸钻系统。它们代表着先进、高效的孔加工技术,通过一次走刀就可以获得精密的加工效果,加工出来的孔位置准确,尺寸精度好;直线度、同轴度高,并且有很高的表面光洁度和重复性。能够方便的加工各种形式的深孔,对于特殊形式的深孔,比如交叉孔、斜孔、盲孔及平底盲孔等也能很