
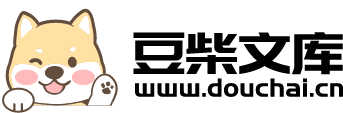
PVC型材挤出工艺.pdf
17****27
在线预览结束,喜欢就下载吧,查找使用更方便
相关资料
PVC型材挤出工艺.pdf
安徽海韵新材料科技有限公司工HYSJ/GY-001艺文件编制:王湘华审核:赵彬批准:李强实施日期:2015.08.201PVC板材生产工艺流程图:配料混料挤出成型▲冷却裁切贴面检验包装入库2“▲”表示质量控制点一、配料工艺:(1)工作期间一定要穿戴工作服,严禁携带任何与工作无关的杂物,以免工作时掉入配料桶内。(2)做好操作前的准备工作,各类助剂应开包检验,原料码放一定要整齐、有序、对号入座。(3)对各类原料的颜色、粒度、流动性(手感)、用量标准一定要十分清楚。(4)不同原料要采用不同精度的计量仪器。用量较
PVC异型材挤出工艺的探讨.doc
冯伟刚PVC异型材挤出工艺是影响产品质量的关键因素之一,应该引起足够的重视。本文结合大量的试验和生产观察数据,从提高PVC异型材产品质量角度出发,量化到角强度、低温落锤冲击等物理性能指标上,探讨PVC异型材的挤出工艺。我们知道,挤出成型工艺是塑料成型加工的一种方式,这种成型特点是:PVC塑料成型从玻璃态——高弹态——粘流态的转变是通过挤出机分区分部加热、剪切挤压来实现的。所谓分区加热,即把挤出机机筒分成1区、2区、3区、4区加热。所谓分部加热,即按机筒、螺杆芯部、模头三部分加热。剪切挤压大小是通过挤出机螺
双螺杆挤出机挤出硬PVC异型材工艺控制.docx
双螺杆挤出机挤出硬PVC异型材工艺控制双螺杆挤出机挤出硬PVC异型材工艺控制摘要:双螺杆挤出机挤出硬PVC异型材工艺在行业中得到广泛应用。本论文对双螺杆挤出机挤出硬PVC异型材工艺的控制进行了研究。首先,介绍了双螺杆挤出机挤出硬PVC异型材的特点和应用,接着分析了控制工艺对产品质量的影响因素,最后提出了相应的工艺控制方法。研究结果表明,通过合理调整挤出机参数和采用先进的控制技术,可以实现硬PVC异型材的高效率和高质量生产。关键词:双螺杆挤出机;硬PVC异型材;工艺控制;产品质量第1节:引言双螺杆挤出机是一
硬PVC异型材的经济快速挤出成型工艺探讨.docx
硬PVC异型材的经济快速挤出成型工艺探讨硬PVC异型材的经济快速挤出成型工艺探讨摘要:PVC(聚氯乙烯)是一种常用的塑料材料,其良好的机械性能和化学稳定性使其广泛应用于各个行业。在许多应用领域中,硬PVC异型材的制造是非常重要的。本论文探讨了硬PVC异型材的经济快速挤出成型工艺,包括挤出设备选择、挤出工艺参数优化和质量控制等方面,旨在提高硬PVC异型材的生产效率和质量。一、引言PVC材料具有良好的机械性能、化学稳定性和成型加工性能,其价格相对较低,因此被广泛应用于各个行业。硬PVC异型材的制造是PVC制品
挤出PVC结皮发泡异型材.doc
挤出PVC结皮发泡异型材HYPERLINK"http://gskbs.blog.163.com/blog/static/16538542008815105942618/"\l"#"pvc专辑2008-09-1510:59阅读95评论0字号:HYPERLINK"http://gskbs.blog.163.com/blog/static/16538542008815105942618/"\l"#"大大HYPERLINK"http://gskbs.blog.163.com/blog/static/