
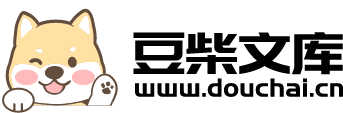
压气机中叶片轮盘耦合结构振动分析.doc
kp****93
在线预览结束,喜欢就下载吧,查找使用更方便
相关资料
压气机中叶片轮盘耦合结构振动分析.doc
压气机中叶片轮盘耦合结构振动分析发表时间:2007-11-6作者:王春洁宋顺广宗晓来源:万方数据关键字:HYPERLINK"http://www.e-works.net.cn/commsearch.aspx?keyword=%ba%bd%bf%d5%a1%a2%ba%bd%cc%ec%cd%c6%bd%f8%cf%b5%cd%b3"\t"_blank"航空、航天推进系统HYPERLINK"http://www.e-works.net.cn/commsearch.aspx?keyword=%d2%b
某型涡轮盘叶片轴的耦合振动分析.docx
某型涡轮盘叶片轴的耦合振动分析涡轮机是一种高速旋转运动的机械设备,其工作原理是利用涡轮盘上的叶片,将高速流体的动能转换为机械能。由于涡轮机的工作环境复杂,很容易发生耦合振动,严重影响涡轮机的运行效率和稳定性。因此,在涡轮机的研究和开发中,对耦合振动问题进行深入的分析和研究具有重要意义。本文将对某型涡轮盘叶片轴的耦合振动问题进行分析,并提出相应的解决方案。一、问题描述某型涡轮盘叶片轴是一种具有高速旋转运动的机械设备,其结构如图1所示:{插入图1}涡轮盘由许多叶片组成,每个叶片均连接到轴上,并用于将高速流体的
轮盘及带叶片轮盘振动分析方法.docx
轮盘及带叶片轮盘振动分析方法轮盘及带叶片轮盘振动分析方法摘要:轮盘及带叶片轮盘是一种常见的机械装置,常用于传输能量、定位和传动。然而,由于其运动过程中的振动问题,会导致整个系统的失效和性能下降。因此,研究轮盘及带叶片轮盘的振动分析方法对于提高系统的性能和稳定性至关重要。本文将介绍轮盘及带叶片轮盘的振动机理、振动分析方法以及实际应用。1.引言轮盘及带叶片轮盘是一种常见的机械装置,广泛应用于各种行业。在使用过程中,由于各种因素,例如不平衡、摩擦、轴向及径向力,轮盘和带叶片轮盘会出现振动问题。这些振动问题不仅会
新型压气机叶片和轮盘连接结构.pdf
新型压气机叶片和轮盘连接结构,解决了传统榫头、榫槽连接结构在轮盘的定位槽内易出现应力集中导致裂纹产生的问题。本发明包括叶片、轮盘和限位环片,叶片具有叶根,叶根具有叶片限位槽;轮盘具有榫槽,限位环片通过螺栓固定在轮盘上。在榫槽内具有轮盘限位通孔,轮盘限位通孔边缘具有限位槽倒角,叶片与轮盘利用叶根与轮盘榫槽进行连接,并且通过叶片限位槽、轮盘限位通孔和限位环片相互配合实现叶片的轴向定位。本发明提供了一种具有动平衡调节能力及较小应力定位槽的压气机叶片轮盘系统,保证机组安全运行的同时,提高了叶片轮盘系统的使用寿命。
基于流固耦合分析的压气机叶片振动特性及寿命预测研究.docx
基于流固耦合分析的压气机叶片振动特性及寿命预测研究一、简述压气机叶片作为航空发动机的关键部件之一,在高压、高温及高速旋转的工作环境下,承受着巨大的气动载荷和机械应力。其振动特性不仅直接影响发动机的稳定性和效率,还关系到叶片的疲劳寿命和可靠性和整体性能。对压气机叶片进行深入的研究和精确的分析具有重要意义。随着计算流体力学和有限元分析技术的快速发展,流固耦合分析逐渐成为研究压气机叶片振动特性的重要手段。通过将流体动力学与固体力学相结合,可以更加准确地模拟叶片在各种工况下的真实受力情况和振动响应,为叶片的设计提