
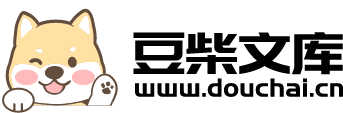
γ-氯丙基三乙氧基硅烷.doc
kp****93
在线预览结束,喜欢就下载吧,查找使用更方便
相关资料
γ-氯丙基三乙氧基硅烷.doc
γ-氯丙基三乙氧基硅烷生产技术综述王正化学工程S141(zyxw)201472187摘要:γ-氯丙基三乙氧基硅烷是合成多种硅烷偶联剂、橡胶等的重要原料,属精细化工产品有广泛的用途。目前使用连续生产氯丙基三乙氧基HYPERLINK"http://www.baidu.com/s?wd=%E7%A1%85%E7%83%B7&hl_tag=textlink&tn=SE_hldp01350_v6v6zkg6"\t"_blank"硅烷的反应系统及其合成方法来生产γ-氯丙基三乙氧基硅烷。它解决了目前氯丙基三乙氧基
氯丙基三乙氧基硅烷在含氯橡胶浅色制品中的应用.docx
氯丙基三乙氧基硅烷在含氯橡胶浅色制品中的应用氯丙基三乙氧基硅烷(略称KH-570)是一种常用的有机硅偶联剂,其化学结构如下所示:[ClCH2CH2CH2Si(OC2H5)3]KH-570在含氯橡胶浅色制品中具有广泛的应用。本文将从KH-570的结构特点、应用效果、工艺条件等方面进行详细探讨。首先,KH-570的结构特点使其具有优异的偶联性能。KH-570分子中的氯丙基可以与含氯橡胶表面的氯乙烯单体形成化学键,实现有机硅分子与橡胶间的共价键连接。而三个乙氧基基团则可以与其他无机颗粒表面的羟基反应生成Si-O
γ-氨丙基三乙氧基硅烷中游离氯含量的检测方法.docx
γ-氨丙基三乙氧基硅烷中游离氯含量的检测方法介绍氨丙基三乙氧基硅烷又称氨丙基三乙氧基硅烷,是一种有机硅单体,具有优异的附着性和耐水性能,被广泛应用于建筑、涂料、纤维处理和印染等领域。但是在氨丙基三乙氧基硅烷的制备过程中,常常会产生游离氯离子,这些离子在应用过程中会对环境和人体健康造成严重的危害,因此检测氨丙基三乙氧基硅烷中游离氯含量的方法非常重要。游离氯(Cl-)是一种无色气体,有刺激性气味,是一种常见的化学元素,广泛应用于工业、农业和医学等领域。游离氯含量的检测方法有许多种,例如化学法、电化学法、光谱法
γ-脲基丙基三乙氧基硅烷的缩合工艺.docx
γ-脲基丙基三乙氧基硅烷的缩合工艺γ-脲基丙基三乙氧基硅烷(γ-Ureidopropyltriethoxysilane)是一种常用的有机硅化合物,具有广泛的应用领域。本论文将介绍γ-脲基丙基三乙氧基硅烷的缩合工艺及其在材料科学和化工领域的应用。1.引言γ-脲基丙基三乙氧基硅烷由于其特殊的结构和属性,在材料科学和化工领域具有重要的应用价值。缩合是一种合成γ-脲基丙基三乙氧基硅烷的常用方法,通过不同的缩合工艺可以调节产物的分子结构和性质。2.γ-脲基丙基三乙氧基硅烷的制备方法2.1.缩合工艺一缩合工艺一使用脲
一种双塔连续酯化生产氯丙基三乙氧基硅烷的系统及方法.pdf
本发明属于化学合成技术领域,具体涉及一种双塔连续酯化生产氯丙基三乙氧基硅烷的系统及方法,系统包括降膜反应器、反应塔、汽提塔、无水乙醇储罐和氯丙基三氯硅烷储罐,反应塔底部设置第一接料釜,汽提塔底部设置第二接料釜;无水乙醇储罐顺次连接气化器、汽提塔、冷凝器A、降膜反应器,氯丙基三氯硅烷储罐连接降膜反应器;降膜反应器顺次连接反应塔、第一接料釜、汽提塔,汽提塔连接反应塔,第二接料釜连接后处理装置。本发明不需要高温高压,不需要中和剂,并且具有耗能低、产品纯度高、收率高、反应周期短、易操作、生产成本低的优点。