
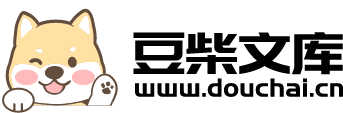
大厚度碳纤维增强树脂基复合材料模压制备方法.pdf
一只****写意
在线预览结束,喜欢就下载吧,查找使用更方便
相关资料
大厚度碳纤维增强树脂基复合材料模压制备方法.pdf
本发明公开了一种大厚度碳纤维增强树脂基复合材料模压制备方法,该方法包括如下步骤:1)制备预浸布:采用碳纤维布和树脂加工制成预浸布;2)预浸布铺层:将预浸布裁剪成设计的形状后,在工装内进行铺层;3)抽真空处理:在预浸布铺层过程中,进行间歇抽真空处理;4)模压固化:铺层结束后,将工装合模放在平板硫化机中进行加压固化;5)后处理:通过机加处理,得到大厚度碳纤维增强树脂基复合材料产品。本发明大厚度碳纤维增强树脂基复合材料模压制备方法可一次模压成型,制备效率高。
树脂基复合材料的制备—模压成型.ppt
树脂基复合材料的制备—模压成型技术主要内容一、模压成型的概念二、模压成型的原料要求三、模压成型工艺1、模压成型的基本原理2、模压成型的工艺条件3、模压成型的工艺过程四、模压成型的优缺点五、模压成型的应用应用实例六、模压成型的发展趋势参考文献谢谢
回收碳纤维增强双马树脂基复合材料的方法.pdf
本发明一种回收碳纤维增强双马树脂基复合材料的方法,属于复合材料回收技术领域;将商用碳纤维增强双马树脂基复合材料置于反应介质乙醇胺溶剂中,然后将溶液升温至140~160℃,恒温反应3~5h。反应结束后,等待反应装置冷却至室温后,将反应后的碳纤维和液体产物通过滤网进行分离,收集碳纤维产物,将收集到的碳纤维产物用无水乙醇清洗数次,以去除碳纤维产物表面的树脂基体残留物和黏附的降解液,随即用去离子水清洗2~3次,将清洗后的碳纤维置于100~110℃烘箱中进行干燥12h,完成对碳纤维增强双马树脂基复合材料的回收。本发
碳纤维‑环氧树脂基复合材料的制备方法.pdf
本发明涉及合成树脂及塑料技术领域,具体涉及一种碳纤维‑环氧树脂基复合材料的制备方法。碳纤维‑环氧树脂基复合材料的制备方法,对PAN基碳纤维表面进行连续阳极氧化处理,阳极氧化处理后除去PAN基碳纤维表面残留的电解质溶液,然后对PAN基碳纤维进行干燥处理;将环氧树脂与三乙烯四胺混合后,将混合溶液均匀涂覆在PAN基碳纤维的表面,在涂覆处理过程中尽量保证纤维两面溶液均匀,随后将其置于金属模具内高温固化,最后将加工成型的复合材料取出,并进行打磨处理除去多余固化物。本发明阳极氧化处理后,PAN基碳纤维的润湿性提高,碳
碳纤维增强树脂基复合材料表面功能涂层制备研究.docx
碳纤维增强树脂基复合材料表面功能涂层制备研究摘要:随着现代工业的发展,碳纤维增强树脂基复合材料在航空、汽车、船舶等领域得到了广泛的应用。然而,其表面易受到身份、摩擦、腐蚀等因素的影响,因此需要为其表面进行功能涂层加工,以提高其抗氧化、耐磨等性能。本文通过文献查阅和样本实验,探讨了几种常见的碳纤维增强树脂基复合材料表面功能涂层制备方法,包括化学气相沉积法、物理气相沉积法、电镀法等,并对其优缺点进行了分析和比较。最后,本文提出了碳纤维增强树脂基复合材料表面涂层的未来发展方向,以期为相关行业的技术研究提供参考。