
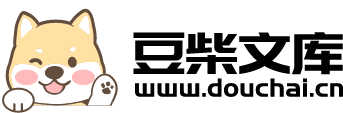
铝银浆生产安全操作规程.doc
是来****文章
在线预览结束,喜欢就下载吧,查找使用更方便
相关资料
铝银浆生产安全操作规程.doc
8铝银浆生产安全操作规程1总则本规程包括铝银浆生产全过程包括球磨、筛分、压滤、抛光、原料及产品运输等工序。2每道工序开始之前首先应认真进行安全检查。检查内容包括以下内容:2.1电器设备金属外壳良好接地电气线路绝缘及防护正常防爆电盘无开启、损坏等不正常现象。2.2机械传动部分润滑良好齿轮咬合、皮带传动等防护装置可靠安装无产生摩擦生热及打火部位等。2.3油浆管道、设备等的静电导除接地装置正常无油浆泄漏现象。2.4接油槽、接料槽、磅秤的铁轮已更换为胶轮无与地面及设备摩擦或打火的可能。
铝银浆生产安全操作规程.docx
铝银浆生产安全操作规程-1--8-铝银浆生产安全操作章程1总则本规程包括铝银浆生产全过程包括球磨、筛分、压滤、抛光、原料及产品运输等工序。2每道工序开始之前首先应当认真进行安全检查。检查内容包括下述内容:2.1电器设备金属外壳良好接地电气线路绝缘及防护正常防爆电盘无开启、损坏等不正常现象。2.2机械传动部分润滑良好齿轮咬合、皮带传动等防护装置可靠安装无产生摩擦生热及打火部位等。2.3油浆管道、设备等的静电导除接地装置正常无油浆泄漏现象。2.4接油槽、接料槽、磅秤的铁轮已更换为胶轮无与地面及设备摩擦
《安全操作规程》之铝银浆生产安全操作规程.doc
此资料由网络收集而来如有侵权请告知上传者立即删除。资料共分享我们负责传递知识。铝银浆生产安全操作规程1总则本规程包括铝银浆生产全过程包括球磨、筛分、压滤、抛光、原料及产品运输等工序。2每道工序开始之前首先应认真进行安全检查。检查内容包括以下内容:2.1电器设备金属外壳良好接地电气线路绝缘及防护正常防爆电盘无开启、损坏等不正常现象。2.2机械传动部分润滑良好齿轮咬合、皮带传动等防护装置可靠安装无产生摩擦生热及打火部位等。2.3
2022《安全操作规程》之铝银浆生产安全操作规程.docx
此资料由网络收集而来,如有侵权请告知上传者立即删除。资料共分享,我们负责传递知识。铝银浆生产安全操作规程1总则本规程包括铝银浆生产全过程,包括球磨、筛分、压滤、抛光、原料及产品运输等工序。2每道工序开始之前,首先应认真进行安全检查。检查内容包括以下内容:2.1电器设备金属外壳良好接地,电气线路绝缘及防护正常,防爆电盘无开启、损坏等不正常现象。2.2机械传动部分润滑良好,齿轮咬合、皮带传动等防护装置可靠安装,无产生摩擦生热及打火部位等。2.3油浆管道、设备等的静电导除接地装置正常,无油浆泄漏现象。2.4接油
2022《安全操作规程》之铝银浆生产安全操作规程.docx
此资料由网络收集而来,如有侵权请告知上传者立即删除。资料共分享,我们负责传递知识。铝银浆生产安全操作规程1总则本规程包括铝银浆生产全过程,包括球磨、筛分、压滤、抛光、原料及产品运输等工序。2每道工序开始之前,首先应认真进行安全检查。检查内容包括以下内容:2.1电器设备金属外壳良好接地,电气线路绝缘及防护正常,防爆电盘无开启、损坏等不正常现象。2.2机械传动部分润滑良好,齿轮咬合、皮带传动等防护装置可靠安装,无产生摩擦生热及打火部位等。2.3油浆管道、设备等的静电导除接地装置正常,无油浆泄漏现象。2.4接油