
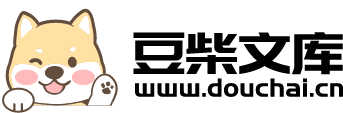
基于机器视觉技术的钢板表面质量检测系统分析.pdf
文库****品店
在线预览结束,喜欢就下载吧,查找使用更方便
相关资料
基于机器视觉技术的钢板表面质量检测系统分析.pdf
基于机器视觉技术的钢板表面质量检测系统分析摘要:近年来,我国的工业化建设的发展迅速,钢铁冶金工业是国民经济的支柱产业,虽然中国是钢铁生产大国,但是中国的各类钢材成品和半成品在质量方面却与发达国家存在明显差距,尤其是钢材产品质量重要组成部分的表面质量,当前钢材主线产品如汽车板、家电板、不锈钢装饰板等,其表面质量对其总体质量乃至市场竞争力起着决定性的作用。利用传统的人工目测方法对钢板表面进行质量检测,极易因为“视觉疲劳”而产生表面缺陷的误报、漏报问题,国内很多钢铁公司都存在这样的情况,更有许多因为钢材表面质量
基于机器视觉技术的钢板表面质量检测系统分析.docx
基于机器视觉技术的钢板表面质量检测系统分析基于机器视觉技术的钢板表面质量检测系统分析摘要:随着工业化的进程和制造业的发展,钢板表面质量检测对于保证产品质量和提高生产效率具有重要意义。本文介绍了基于机器视觉技术的钢板表面质量检测系统的原理和关键技术。首先,介绍了机器视觉技术在钢板表面质量检测中的应用背景和意义。然后,详细阐述了钢板表面缺陷的识别和评估方法,包括特征提取、分类算法和评估指标等。最后,给出了钢板表面质量检测系统的实验结果和性能分析,总结了该系统的优点和不足之处,并展望了未来针对钢板表面质量检测系
基于机器视觉的瓷砖表面质量分析与检测.pdf
第32卷第1期西安建筑科技大学学报Vol.32No.12000年3月J1Xi’anUniv.ofArch.&Tech.Mar.2000基于机器视觉的瓷砖表面质量分析与检测赵海洋1,冯心海2,薛钧义1,江显异3(11西安交通大学,陕西西安710049;21佛山科学技术学院,广东佛山528000;31佛山钻石陶瓷企业集团,广东佛山528000)摘要:提出了基于平面CCD的瓷砖产品的表面质量检测的准则与方法.首先对瓷砖产品的缺陷特征进行分类,得到两大类结构特征——斑点结构和广义线性结构,针对这两种几何特征,本文
基于机器视觉的金刚线表面质量检测.pptx
汇报人:/目录0102机器视觉的定义和原理机器视觉在质量检测中的应用机器视觉技术的优势和局限性03金刚线的定义和用途金刚线表面质量对产品质量的影响金刚线表面质量检测的意义和重要性04系统组成和工作原理图像采集和处理技术表面缺陷检测算法和分类识别技术检测精度和可靠性分析05实验设备和样本选择实验结果分析和对比性能评估和优化建议06基于机器视觉的金刚线表面质量检测的优势和应用前景需要进一步研究和解决的问题对未来发展的展望和研究方向汇报人:
基于机器视觉的钢板焊缝缺陷检测方法研究.docx
基于机器视觉的钢板焊缝缺陷检测方法研究摘要钢板焊缝缺陷检测一直是机械制造行业关注的焦点问题,而机器视觉技术的发展为此提供了有效的解决途径。本文研究了基于机器视觉的钢板焊缝缺陷检测方法。首先,介绍了钢板焊缝缺陷检测相关技术和国内外研究现状。其次,针对钢板焊缝的三个典型缺陷——焊缝凸包、焊缝开裂和缺陷孔洞,提出了对应的检测算法。最后,通过实验验证了本文所提出算法的可行性和有效性。关键词:机器视觉,焊缝缺陷检测,焊缝凸包,焊缝开裂,缺陷孔洞一、介绍钢板焊缝作为机械制造行业集成化程度日益增高的关键制造工艺之一,其