
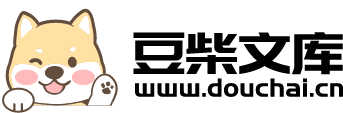
FMEA生活中电子教案.ppt
天天****心情
亲,该文档总共135页,到这已经超出免费预览范围,如果喜欢就直接下载吧~
相关资料
FMEA生活中电子教案.ppt
FMEA生活中有个小孩在爬墙推倒FMEA是一种使用十分普遍的思维方法日常生活中几乎每人都在使用这种方法问题在于:自觉与不自觉科学法则与自然法则注意性与随意性借鉴型与抛弃型螺旋提高与闭环解决介绍二个定理介绍二个定理AAA回顾二个定理很明显:过程的改进与优化流程设计和流程图ProcessDesignandProcessFlowChart流程设计和流程图ProcessDesignandProcessFlowChart510.用文字规范程序,形成文件开始把取得的成果规范化形成标准化合适的管理文件成为大家共同遵守的
汽车电子FMEA经典教案.ppt
............................................................................................................
电子工程中FMEA实施的作用和途径.docx
电子工程中FMEA实施的作用和途径电子工程中FMEA实施的作用和途径FMEA即潜在失效模式与后果分析,通常在电子工程行业能够有效实施的模式并不多,但出现失效模式的原因有很多种,最主要的原因还是因为电子工程设计问题。为减少产品潜在的风险隐患,一般设计人员根据技术标准来操作FMEA,对电子生产各个部件进行了检测和评估,以便提高电子产品的质量与安全。但往往在制定FMEA环节,设计人员无法对电子产品的安全性、维修性、测试性等做出保证,其测试结果和作用也存在较多不可预知的影响。因此,只有制定清晰的作用与技术方法指导
汽车电子FMEA培训.ppt
欢迎参加五大手册培训--FMEA--APQP策划包括5个阶段过程:所有阶段的输入和输出都是建议性的;输入和输出应根据产品、过程和顾客满意及期望的适用性确定;输入用于早期活动;输出是活动的结果;超出要求的输出由顾客和/或供方确定。APQP策划包括的5个阶段过程1.0计划一、五项核心工具与APQP的关联五项核心具当前适用版本五项核心具当前适用版本五项核心具当前适用版本APQP(先期产品质量策划)流程二、FMEA---潜在的失效模式和影响分析FMEA发展FMEA及其目的有效实施FMEA的效益对组织和
FMEA及其在航空电子产品中的应用.docx
FMEA及其在航空电子产品中的应用FMEA及其在航空电子产品中的应用FMEA即故障模式及影响分析(FailureModeandEffectsAnalysis),是一种旨在预测和减少产品或过程故障的技术,也是一种经验教训的总结方式。FMEA通常用于验证设计或制造过程中的措施,并针对潜在故障对其进行优化。在航空电子产品的设计、生产和维护过程中,FMEA起到了至关重要的作用。在航空电子产品设计过程中使用FMEA,可以帮助设计师更好地确定产品的功能、特点和风险。通过考虑可能发生的故障模式和其对安全和性能的影响,设