
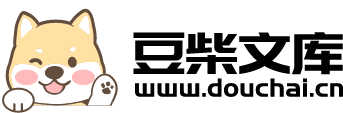
型腔的数控加工工艺.docx
映雁****魔王
在线预览结束,喜欢就下载吧,查找使用更方便
相关资料
型腔的数控加工工艺.docx
拟加工型腔类零件图待加工的零件是一个典型的带型腔的凸台零件整体为凸台中间带有型腔。具体形状如图1所示。图1零件图的工艺分析首先分析一下尺寸标注方法。零件图上尺寸标注的方法为同一基准标注适应了数控加工零件的特点。18mm8mm6mm三个尺寸是以上表面为设基金准80mm72mm71.5mm40mm是以原点O为设计基准。这种标注方法便于编程、又利于设计基准、工艺基准和编程原点的同一。但是尺寸40mm不便于测量应以圆弧的直径端为终端标注为60mm。其次进行零件图的完整性与正确性进行分析。零件尺寸标准完整各部位都能
型腔的数控加工工艺.docx
拟加工型腔类零件图待加工的零件是一个典型的带型腔的凸台零件,整体为凸台,中间带有型腔。具体形状如图1所示。图1零件图的工艺分析首先,分析一下尺寸标注方法。零件图上尺寸标注的方法为同一基准标注,适应了数控加工零件的特点。18mm,8mm,6mm三个尺寸是以上表面为设基金准,80mm,72mm,71.5mm,40mm是以原点O为设计基准。这种标注方法便于编程、又利于设计基准、工艺基准和编程原点的同一。但是尺寸40mm不便于测量,应以圆弧的直径端为终端,标注为60mm。其次,进行零件图的完整性与正确性进行分析。
型腔的数控加工工艺.docx
拟加工型腔类零件图待加工的零件是一个典型的带型腔的凸台零件,整体为凸台,中间带有型腔。具体形状如图1所示。图1零件图的工艺分析首先,分析一下尺寸标注方法。零件图上尺寸标注的方法为同一基准标注,适应了数控加工零件的特点。18mm,8mm,6mm三个尺寸是以上表面为设基金准,80mm,72mm,71.5mm,40mm是以原点O为设计基准。这种标注方法便于编程、又利于设计基准、工艺基准和编程原点的同一。但是尺寸40mm不便于测量,应以圆弧的直径端为终端,标注为60mm。其次,进行零件图的完整性与正确性进行分析。
型腔的数控加工工艺.docx
拟加工型腔类零件图待加工的零件是一个典型的带型腔的凸台零件,整体为凸台,中间带有型腔。具体形状如图1所示。图1零件图的工艺分析首先,分析一下尺寸标注方法。零件图上尺寸标注的方法为同一基准标注,适应了数控加工零件的特点。18mm,8mm,6mm三个尺寸是以上表面为设基金准,80mm,72mm,71.5mm,40mm是以原点O为设计基准。这种标注方法便于编程、又利于设计基准、工艺基准和编程原点的同一。但是尺寸40mm不便于测量,应以圆弧的直径端为终端,标注为60mm。其次,进行零件图的完整性与正确性进行分析。
模具型腔数控铣削加工工艺优化.doc
TECHNOLOGY科技纵横2010.4CHINAEQUIPMENT【摘要】本文介绍了模具型腔数控铣削加工工艺优化。【关键词】模具型腔数控加工工艺优化设计引言模具型腔数控铣削加工工艺流程:粗铣→半精铣→精铣→清角。影响型腔数控铣削工艺方案选择的因素有很多,主要有加工材料、加工方法、加工设备、走刀方式、刀具参数、切削用量、加工精度、加工余量、装夹方式、下刀位置、进退刀方式等等,本文重点就工艺参数优化进行探讨。1.铣削参数与铣削刀具1.1数控加工的铣削参数粗加工为体积加工,从高的生产率考虑,应在保证刀具耐用度