
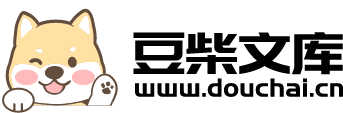
硫磺回收装置的能耗分析及节能措施.pdf
qw****27
在线预览结束,喜欢就下载吧,查找使用更方便
相关资料
硫磺回收装置的能耗分析及节能措施.pdf
炼油技术与工程2007年2月PETROLEUMREFINERYENGINEERING第37卷第2期能t利用硫磺回收装置的能耗分析及节能李背蓄中国石油集团华东设计院(山东省青岛市266071)要:通过某摘些引进装置的设计能耗、单位能耗及各项公用工程在装置能耗中所占比例等一系列数据,分别从装置产生的能量和消耗的能量进行逐项分析。提出了硫磺回收部分应采用合适的焚烧温度,利用凝结水代替除氧水,减少外供除氧水量,节约电耗;尾气处理部分应减少蒸汽耗量,降低电耗量;合理选择加热方式,降低燃料气用量;调整急冷水、贫液和酸
硫磺回收装置的能耗分析和节能措施.pdf
͙โ㘩⎼じࢣじኯኯ$)*/"'03&*(/&/&3(:Ꭰᰴ㞮㘩ᩫも̺ឬᱛஅᜈᎵᄉᑞᏱѫౡ֖ᓫᑞଏஶٿᆴᇠᱺ㣭㣭͙ⴟ⇥ࡺ͈䃪䃍䮎ᖇᆝ͈䱾ᇇ⼷㷱㒚㘩㕃͙ᝬࢌ℀ҷふ̬㈧݃ᢚᖇܲݗϺ㷱㒚ϓ⩋⮰⩔ژर䶥ܜࢁѹ㘩㕃ܜᦄ㺭䕆䓳χᑁ䔇㷱㒚⮰䃪䃍㘩㕃㘩䛻স⊴㕃⮰㘩䛻䔼䶥䔇㵸ܲᖇₐദ̶ܦर㞮㘩ᣖᤗ䩚䃹⸦ఊᩢ㘩㕃ܲ㞮㘩ᣖڟϓݹ㼬㷱㒚⮰䃪䃍㘩㕃⊵ߟࣹᏀ䛶ᩪᵥᢚტ㏻䉤ༀ䶭ࣽ⮰ⴟ⇥ࡂ䃪䃍㘩䛻ٷуᝬঔⴑᖇ⩝κ⸦ఊᩢ㷱㒚☙㘩⮰㑄ᩱᖇ⸦ఊᩢ㷱㒚᭛◨⇥㷱㒚͙ᘋ̬̹⊴
硫磺回收装置的堵塞分析与预防措施.docx
硫磺回收装置的堵塞分析与预防措施硫磺回收装置的堵塞分析与预防措施摘要:硫磺回收装置在硫磺生产过程中起到了关键的作用。然而,由于硫磺回收装置的工作环境特殊,它很容易堵塞。本文通过对硫磺回收装置堵塞原因的分析,总结出了预防堵塞的措施,为硫磺生产过程的顺利推进提供了参考。1.引言硫磺是一种重要的化学原料,在许多工业领域有着广泛的应用。然而,在硫磺的生产过程中,大量的硫磺被释放为废气,造成了严重的污染。为了解决这个问题,硫磺回收装置应运而生。它能够有效地回收硫磺废气,减少了对环境的影响。但是,由于硫磺回收装置工作
硫磺回收装置腐蚀机理分析及防护措施.docx
硫磺回收装置腐蚀机理分析及防护措施硫磺回收装置是一种重要的工业设备,在石化、化工、煤化等行业中广泛应用。然而,由于硫磺气体中含有较高的酸性成分,硫磺回收装置很容易受到腐蚀的影响,从而影响设备的使用寿命和性能。因此,本文将对硫磺回收装置腐蚀机理进行分析,并提出相应的防护措施,以期为相关行业提供一定的参考。一、硫磺回收装置腐蚀机理分析硫磺回收装置腐蚀机理主要表现为酸性腐蚀和氧化腐蚀。其中酸性腐蚀是由硫磺气体中的氧化硫和水分反应产生的硫酸或硫酸化合物造成的,主要对装置的金属表面产生腐蚀破坏。而氧化腐蚀则是由于硫
糠醛精制装置的能耗分析及节能措施.docx
糠醛精制装置的能耗分析及节能措施糠醛精制装置的能耗分析及节能措施摘要:随着人们对可再生能源的重视以及环境保护的日益加强,糠醛作为一种具有潜在利用价值的废弃物,得到了广泛关注。糠醛精制装置是将糠醛经过一系列的分离、精炼和处理工艺,使其转化为有经济价值的产品的装置。然而,糠醛精制装置在运行过程中能耗较高,给环境带来一定的负担。本文通过能耗分析,探讨了糠醛精制装置中能耗较高的原因,并提出了相应的节能措施,以期减少能源消耗,提高装置的经济性和环境友好性。1.引言糠醛是由农作物秸秆在高温下分解制备而成的一种废弃物。