
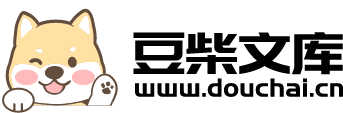
航空发动机典型产品燃烧室机匣加工工艺分析和技术应用.pdf
文库****品店
在线预览结束,喜欢就下载吧,查找使用更方便
相关资料
航空发动机典型产品燃烧室机匣加工工艺分析和技术应用.pdf
航空发动机典型产品燃烧室机匣加工工艺分析和技术应用本文从某型航空发动机燃烧室机匣的工艺特点出发,结合企业能力现状,对燃烧室机匣的加工工艺进行分析,并在应用过程中结合数控加工装备、三维CAD/CAM软件应用技术进行试验,取得一定的经验和效果。分享此类型薄壁燃烧室机匣的开发研制过程中可供借鉴的工艺方法和应用技术。一、前言航空发动机机匣是发动机中的壳体、框架类静子部件,是发动机的重要承力部件。主要作用是承载发动机零组件重量、承受轴向和径向力,构成气流通道,包容气流、发动机转子,防止转子叶片断裂飞出,起到连接、支
航空发动机燃烧室机匣铣加工工艺优化研究.docx
航空发动机燃烧室机匣铣加工工艺优化研究航空发动机燃烧室机匣铣加工工艺优化研究摘要:随着航空工业的快速发展,航空发动机作为飞机的核心部件之一,其性能和质量要求也越来越高。燃烧室是航空发动机中一个关键的部件,其内部的结构和加工工艺对发动机的性能具有重要影响。本文着重研究航空发动机燃烧室机匣的铣加工工艺优化,旨在提升发动机的性能和质量。1.引言航空发动机燃烧室机匣作为连接各个关键部件的重要部分,在发动机的运行中承受着高温、高压和高速的工作环境。因此,机匣的质量和性能对于发动机的整体性能至关重要。铣加工是机匣制造
燃烧室前端机匣铣加工工艺研究.docx
燃烧室前端机匣铣加工工艺研究燃烧室前端机匣是燃气涡轮发动机中的一个重要部件,其主要功能是引导空气和燃料混合物进入燃烧室中进行燃烧,同时要承受高温高压下的冲击和振动。因此,对燃烧室前端机匣的加工工艺进行研究具有极其重要的意义,可以提高产品的质量和性能,同时提高生产效率,降低成本。一、燃烧室前端机匣的加工工艺1.加工设备的选择燃烧室前端机匣的加工难度较大,需要使用高精度的加工设备和工具,以保证加工精度和表面质量。常用的加工设备包括数控铣床、线切割机、数控磨床等。2.加工用料的选择燃烧室前端机匣主要使用高温合金
航空发动机燃烧室机匣铣加工工艺优化研究的任务书.docx
航空发动机燃烧室机匣铣加工工艺优化研究的任务书任务书课题名称:航空发动机燃烧室机匣铣加工工艺优化研究任务背景:随着飞机工业的发展,航空发动机作为航空工业的核心之一,其关键部件燃烧室机匣的铣加工工艺也发挥着极其重要的作用。目前,我国的航空工业正处于快速发展的阶段,而发动机行业也是在全面推进自主创新和发展轻量化、高寿命等方面的工作,发动机燃烧室机匣铣加工工艺也面临着新的需求和挑战。因此,本课题拟通过对燃烧室机匣铣加工工艺优化进行研究,为航空工业的发展提供有力的支持和保障。任务目标:通过对燃烧室机匣铣加工工艺进
航空发动机机匣加工工艺研讨.docx
航空发动机机匣加工工艺研讨一、引言航空发动机机匣是发动机的重要组成部分,在整个发动机的设计与制造中起到了至关重要的作用。机匣的质量与性能不仅直接影响航空发动机的安全性能,还关系到整个飞行器的运行安全性和经济性。因此,对航空发动机机匣的加工工艺研讨具有重要意义。二、航空发动机机匣的特点和制造要求机匣是航空发动机的骨架部分,它不仅要承受各种作用力,而且还要承受高温、高压等复杂的工作环境,因此机匣制造需要满足一些特殊要求:1.高强度:机匣需要承受发动机本身的重量和飞行时的极端负载,因此机匣的强度要求非常高。2.