
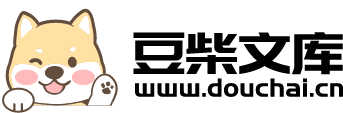
绞盘内齿环精锻塑性成型工艺.pdf
书生****35
在线预览结束,喜欢就下载吧,查找使用更方便
相关资料
绞盘内齿环精锻塑性成型工艺.pdf
本发明公开了一种绞盘内齿环精锻塑性成型工艺,包括以下步骤:①温锻塑性成型:将实心圆柱形金属坯料加热至锻造温度,模锻出两端面内陷共底各自成盲孔结构的装配端和预留挤压内齿坯料;②机加工去底,形成通孔结构,底所对应的部分称为装配端和预留挤压内齿坯料的结合部;③冷锻塑性成型:在冷锻成型凹模中,利用齿形模将预留挤压内齿坯料内壁或预留挤压内齿坯料和结合部的内壁模锻出内齿齿形。该工艺生产效率高、生产成本低,生产的产品的齿面强度和精度高,尤其是经挤压产品质量稳定,综合机械性能高,能满足起重设备绞盘使用,符合当今世界制造业
过滤器壳体精锻塑性成型生产工艺.pdf
本发明公开了一种过滤器壳体精锻塑性成型生产工艺,包括以下步骤:①温锻塑性成型;②井式炉退火、内外圆车加工、抛丸、前处理;③精整成型;④终端取长。该工艺生产的产品质量稳定、成品率高、生产周期短、生产效率高,替代了热锻后大量采用机床加工的加工方法,减少了机床加工的作业量,节省了原材料,既能满足精度要求,又降低了制造成本及周期,同时也符合当今世界制造业发展的趋势。
圆柱齿轮温冷复合精锻塑性成型工艺.pdf
本发明公开了一种圆柱齿轮温冷复合精锻塑性成型工艺,包括以下步骤:①温锻塑性成型;②正火、整形、喷砂、磷化、皂化表面及处理;③冷锻塑性成型;④等温正火后利用高速园盘锯对圆柱齿轮坯料冷锻件按尺寸分割;⑤冷推挤精整成型。该工艺生产的产品质量稳定、生产效率提高、生产周期较短,替代了热锻后大量采用机床加工的加工方法,减少了机床加工的作业量,既能满足精度要求,又降低了制造成本及周期,同时也符合当今世界制造业发展的趋势。
弧齿锥齿轮塑性成型工艺研究.docx
弧齿锥齿轮塑性成型工艺研究标题:弧齿锥齿轮塑性成型工艺研究摘要:随着工业化的发展和科学技术的进步,弧齿锥齿轮作为一种重要的传动元件在机械制造领域得到广泛应用。塑性成型作为一种新型的成型方法,以其高效、快捷和成本低等优势受到了广泛关注。本文通过对弧齿锥齿轮塑性成型的相关工艺进行研究和探讨,旨在对弧齿锥齿轮塑性成型工艺进行深入了解和优化,以提高弧齿锥齿轮的加工精度和性能。第一章引言1.1研究背景1.2研究目的与意义第二章弧齿锥齿轮的塑性成型工艺介绍2.1塑性成型的概念和发展历程2.2弧齿锥齿轮的结构和应用2.
直齿内齿轮精锻成形工艺数值模拟及实验研究.docx
直齿内齿轮精锻成形工艺数值模拟及实验研究一、简述话说在我们的机械世界里,齿轮扮演着举足轻重的角色。它们就像是一个个小小的指挥家,协调着各种设备的运转。而直齿内齿轮,作为齿轮家族中的一员,更是有着不可替代的地位。那么如何让这些直齿内齿轮更加完美地为我们服务呢?答案就是——精锻成形工艺。精锻成形工艺是一种通过精确计算和模拟,对金属材料进行加工的方法。它可以使金属材料在一定程度上消除内部缺陷,提高材料的强度和韧性,从而达到提高产品质量的目的。而直齿内齿轮精锻成形工艺,就是在这样的背景下应运而生的。为了更好地研究