
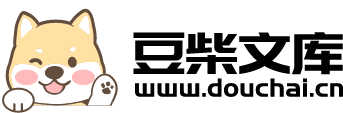
电池箱结构优化设计方法.pdf
书生****12
在线预览结束,喜欢就下载吧,查找使用更方便
相关资料
电池箱结构优化设计方法.pdf
本发明提供一种电池箱结构优化设计方法,包括以下步骤:(1)建立拓扑优化模型;(2)拓扑优化,确定电池箱内部梁结构及外部固定点位置;(3)形状优化,确定电池箱内部梁截面尺寸;(4)自由尺寸优化,确定电池箱内部梁厚度尺寸;(5)拓扑优化,确定电池箱内部梁焊点数量和布置方式;(6)形貌和尺寸优化,确定电池箱箱盖布筋方式;(7)将优化结构解释成CAD模型。该方法提出了直接用于指导电池箱结构优化设计的方法并形成了完整的优化设计流程,可以用于实现电池箱结构的定量设计,避免盲目试错,缩短开发周期,具有较大的工程实用价值
一种电动汽车电池箱的结构优化设计.pptx
电动汽车电池箱的结构优化设计目录添加目录项标题电动汽车电池箱结构优化的重要性提高电池安全性增强电池可靠性降低生产成本提升电池寿命电动汽车电池箱结构优化的主要方法电池箱体设计优化电池管理系统优化冷却系统优化电池箱振动与冲击性能优化电动汽车电池箱结构优化的实施步骤明确优化目标进行结构分析制定优化方案实施优化方案优化效果评估电动汽车电池箱结构优化的未来展望智能化设计技术的应用新型材料的应用电池箱结构与整车性能的协同优化绿色制造与可持续发展感谢观看
纯电动汽车铝合金电池箱结构优化设计.docx
纯电动汽车铝合金电池箱结构优化设计随着纯电动汽车的快速发展,电池箱成为了电动汽车的一个重要部件。电池箱不仅需要具备良好的机械稳定性和耐久性,也需要满足一定的重量要求以及热管理能力。铝合金材料因其相对较轻的质量和较高的强度,成为了电池箱材料的首选。本文旨在探讨纯电动汽车铝合金电池箱结构优化设计。首先,将介绍铝合金材料的一些特性和常见的加工方式,然后,将探讨电池箱的设计要素以及相应的结构优化方法,最后,将给出一个具体的案例,说明如何通过结构优化设计来实现更好的性能指标。一、铝合金材料铝合金材料是由纯铝和其他元
基于Optistruct的FSEC赛车电池箱轻量化结构设计及优化.docx
基于Optistruct的FSEC赛车电池箱轻量化结构设计及优化论文题目:基于Optistruct的FSEC赛车电池箱轻量化结构设计及优化摘要:随着电动汽车(EV)和混合动力汽车(HEV)在市场上的普及,电池箱的轻量化设计和优化成为了研究的热点。本文以FormulaStudentElectricChina(FSEC)赛车电池箱为研究对象,利用Optistruct软件进行轻量化结构设计及优化。首先,对电池箱进行结构仿真,确定初始设计。然后,利用有限元分析,优化电池箱结构,以提高其强度和刚度,同时减轻重量。最
基于Optistruct的FSEC赛车电池箱轻量化结构设计及优化.pptx
,目录PartOnePartTwo有限元分析软件结构优化算法轻量化设计应用电池箱结构设计需求PartThree电池箱整体结构电池箱材料选择电池箱散热设计电池箱安全性能要求PartFour结构优化设计流程拓扑优化技术应用轻量化材料选择电池箱结构优化结果PartFive优化前后性能对比轻量化效果评估结构强度与刚度分析优化方案可行性评估PartSix在赛车领域的应用前景在其他领域的应用潜力技术发展对轻量化设计的影响未来研究方向与展望THANKS