
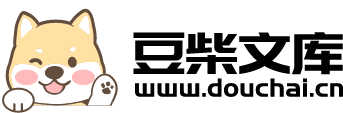
一种高效节能环保的复合型高温箱式电炉.pdf
Ch****49
在线预览结束,喜欢就下载吧,查找使用更方便
相关资料
一种高效节能环保的复合型高温箱式电炉.pdf
一种高效节能环保的复合型高温箱式电炉,其特征是它包括为耐火材料炉膛(1)和耐火纤维隔热层(2),所述耐火材料炉膛(1)置于耐火纤维隔热层(2)内。所述耐火材料炉膛(1)内设有发热体(3);所述发热体(3)为电热丝、碳棒、硅碳棒或硅钼棒。本发明采用薄壁炉膛,热容小,解决了厚壁炉膛电炉蓄热损耗高导致设备能耗高、升降温速度慢的问题,本发明的耐火材料炉膛可同时满足耐火度和强度要求;本发明采用氧化铝、氧化锆空心球耐火材料,刚玉-莫来石质耐火材料等,解决了耐火纤维炉膛不能应用于高温、粉化后产生有害纤维粉尘的问题,本发
箱式电炉节能探讨.docx
箱式电炉节能探讨标题:箱式电炉节能探讨引言:随着环境污染问题的日益严重,节能成为了全球共同面临的挑战。电力作为一种清洁能源,正逐渐在工业领域得到广泛应用。箱式电炉作为一种常见的工业设备,其节能性能尤为重要。本文将探讨箱式电炉的节能优势,并提出一些提高其节能性能的建议。一、箱式电炉的节能优势1.1高能效:箱式电炉以电能为能源,在能量转换过程中没有烟尘、废气等污染物的排放,相比传统燃烧方式能够实现能源的高效利用。1.2温度控制精确:箱式电炉的加热控制系统采用先进的自动化技术,能够精确控制工作温度,实现能源的精
一种炉门升降式全纤维炉膛高效节能高温电炉.pdf
本发明公开了一种炉门升降式全纤维炉膛高效节能高温电炉,包括炉体,所述炉体的侧壁上开设有炉膛入口,所述炉体的侧壁上开设有滑槽,所述滑槽内滑动连接有炉门,所述炉体的侧壁上开设有机构槽,所述炉体的内底部开设有凹槽,所述凹槽内滑动连接有放置箱,所述放置箱的内壁上固定连接有多个支撑板。本发明通过设置锥齿轮机构和螺纹杆机构,旋转手轮会驱动主动锥齿轮转动,进而从动锥齿轮会带动螺纹杆转动,滑块会随着螺纹杆的转动而沿竖直方向运动,滑块可带动炉门实现开启或关闭;这种情况下,可使得炉门在竖直方向上实现升降式关闭,与传统的旋转式
高温电炉节能改造.docx
高温电炉节能改造高温电炉节能改造摘要:随着能源消耗的不断增加和环境问题的日益严重,节能技术已经成为各领域研究的热点之一。高温电炉作为工业生产中常用的设备之一,其能耗对于企业的经济效益和环境负担有着重要影响。本文将针对高温电炉进行节能改造的方法和措施展开研究,旨在提供一定的参考和指导。引言:高温电炉是一种能够提供高温热能的设备,广泛应用于冶金、玻璃、陶瓷等行业。然而,由于其能耗较高,对于企业而言,使用高温电炉不仅意味着大量的电费支出,同时也对环境造成了不可忽视的压力。因此,对高温电炉进行节能改造已经成为一种
炉门升降式全纤维炉膛高效节能高温电炉.pdf
本发明公开了一种炉门升降式全纤维炉膛高效节能高温电炉。本发明在炉体结构设计、炉膛材料选择和温度控制方面与传统电炉相比创新优势明显:炉门在底部,通过丝杠控制升降,炉门降下后可在其上面摆放煅烧样品,摆放方便且装载量多,炉门上升关闭后,密封性极好,不易从炉口散热;采用多层梯度耐温全纤维炉膛,隔热性能优异,蓄热量少,电炉节能效果十分显著,升降温迅速;独特的炉顶拼装结构设计使其不易坍塌;发热体四面加热,炉内温场均匀;温控系统先进、操作简便,采用PID智能控温仪表,采用智能电力显示仪表,集中显示运行电压、电流、功率、