
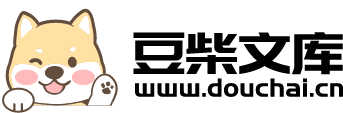
一种热辐射原位制备VC涂层的方法.pdf
Th****s3
在线预览结束,喜欢就下载吧,查找使用更方便
相关资料
一种热辐射原位制备VC涂层的方法.pdf
本发明涉及热辐射处理,具体指一种热辐射原位制备VC涂层的方法,在模具钢和工具钢表面原位制备超硬VC(碳化钒)涂层,属于先进材料制备领域。制备方法为:热辐射处理的盐浴成分质量百分比:85%的基盐-无水硼砂、3%FeSi45、9%FeV50和3%NaF,先用无水硼砂基盐启动盐炉,加热至750℃左右,等基盐完全熔化后,再将供钒剂、活化剂和还原剂按上的比例混合均匀后,加入到熔化的基盐中,然后将其组成的盐浴加热至1200-1250℃,再将模具钢或工具钢的试样放入盐浴中,保温6h,取出后取出在油中淬火,180~200
一种银功能涂层原位制备方法.pdf
本发明公开了一种银功能涂层原位制备方法,对固态纳米Ag表面进行超声分散改性,获得纳米Ag浆料;将所述纳米Ag浆料涂覆在零件基体表面,干燥后获得纳米Ag颗粒涂层;将干燥后的具有纳米Ag颗粒涂层的零件置于保护气氛中,在温度为200℃~450℃下保温后随炉冷却,完成改性剂的催化分解与所述纳米Ag颗粒的原位晶化,获得Ag涂层。该方法可以有效避免电镀银产生的含氰镀液环境污染问题;Ag涂层与基体界面具有冶金结合特性,提高了界面结合强度;其制备方法工艺适应性强、工艺简单适合广泛推广。
一种原位合成制备复合热障涂层的方法.pdf
本发明公开了一种原位合成制备复合热障涂层的方法,将R2O3和ZrO2粉体混合球磨后的R2O3/ZrO2混合粉末和YSZ粉末混合;用等离子喷涂方法喷涂在高温合金基体上的粘结层表面,然后置于电阻炉中,在空气条件,1000-1400°C下进行烧结,制备出R2Zr2O7弥散分布的YSZ陶瓷层。由本发明方法制备的陶瓷层消除了R2Zr2O7稀土锆酸盐陶瓷层与YSZ陶瓷层的层界面,使得热障涂层具有高温相稳定性,与传统的YSZ相比具有较低的热导率,且降低了陶瓷层的透氧率;与单纯的稀土锆酸盐陶瓷层相比使用寿命增长,可以满足
一种低成本纳米原位颗粒增强钛合金耐磨涂层制备方法.pdf
本发明公开了一种低成本纳米原位颗粒增强钛合金耐磨涂层制备方法,解决现有技术中钛合金的耐磨性较差的问题。该涂层制备方法的制备步骤如下:(1)利用行星式快速研磨机制备Al?Si基多元合金粉体;(2)利用激光沉积设备在钛合金表面沉积Al?Si基多元合金耐磨涂层。在沉积过程中采用循环气体进行冷却,以增加熔融涂层的冷却速度,保证涂层中纳米原位颗粒增强相的生成;(3)利用机加工技术在激光沉积耐磨涂层表面切掉多余涂层,剩留耐磨涂层厚度距钛合金基体0.3?0.5mm;(4)利用减薄与研磨技术将剩留耐磨涂层继续减薄与研磨,
抗光热辐射纳米复合织物涂层材料及其制备方法.pdf