
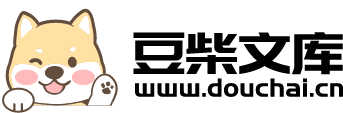
基于化学活化的剑麻炭纤维制备锂离子电池负极材料的方法.pdf
闪闪****魔王
在线预览结束,喜欢就下载吧,查找使用更方便
相关资料
基于化学活化的剑麻炭纤维制备锂离子电池负极材料的方法.pdf
本发明公开了一种基于化学活化的剑麻炭纤维制备锂离子电池负极材料的方法。将剑麻纤维揉搓、洗涤和烘干;用质量分数为15-25%的ZnCl2溶液按ZnCl2和剑麻纤维的质量比为2-6:1浸渍比浸泡24小时,用去离子水冲洗,80-100℃经12-24小时烘干;置于真空管式电阻炉中,在气体流量为40ml/min的氮气气氛下炭化0.5-1小时,炭化温度为700-1000℃,升温速率为1-10℃/min,自然冷却后即获得黑色纤维状剑活性炭纤维。以锂片为正极材料、以制得的剑麻活性炭纤维经研磨后做为负极材料组装成锂离子电池
锂离子电池用中空炭纤维负极材料及其制备方法和应用.pdf
本发明公开了一种锂离子电池用中空炭纤维负极材料及其制备方法和应用,该锂离子电池用炭纤维负极材料的微观形貌呈中空纤维状。制备方法包括(1)将生物质原材料浸入硝酸溶液中在60℃~90℃下进行脱木质素处理,得到悬浮液;(2)将所得悬浮液超声分散后过滤干燥,得到原生木质纤维,再在惰性气体保护下升温至700℃~1100℃进行热解炭化即得炭纤维负极材料。本发明的负极材料较好地保留了中空纤维状形貌,具有比容量大、倍率性能优异的特点。本发明的制备方法原材料来源丰富、环保可再生,可广泛应用于锂离子电池制备领域。
锂离子电池用生物质炭纤维负极材料及其制备方法和应用.pdf
本发明公开了一种锂离子电池用生物质炭纤维负极材料及其制备方法和应用,该锂离子电池用生物质炭纤维负极材料的微观形貌呈纤维状,生物质炭纤维的直径为1μm~5μm。制备方法包括(1)将生物质原材料浸入碱溶液中在120℃~180℃下进行水热预处理,得到悬浮液;(2)将所得悬浮液过滤得到前驱体,前驱体超声分散后过滤干燥,再在惰性气体保护下升温至700℃~1100℃进行热解炭化即得负极材料。本发明的负极材料较好地保留了纤维状形貌,首次库伦效率高,比容量大,制备方法原料来源丰富,环保可再生,且工艺过程简单,可广泛应用于
负极材料及制备方法、锂离子电池负极、锂离子电池及制备方法、锂离子电池包.pdf
本发明公开了一种负极材料,包括硅基材料,以及覆盖于所述硅基材料上的含硫锂盐添加物,所述含硫锂盐添加物在外界机械力的作用下均匀分散在所述硅基材料表面,所述含硫锂盐添加物与所述硅基材料的质量比为(1:10)~(1:200),所述硅基材料包括硅、硅氧化物、硅合金中的任一种,所述硅基材料不具有特殊核壳结构但具有丰富的微介孔结构,所述含硫锂盐添加物为含硫的锂盐衍生物,纯度≥98%。本发明采用含硫锂盐添加物对硅基材料表面进行组份调控,能够增加界面内层SEI膜无机层,提高材料界面膜的稳定性,改善硅基材料的首周库仑效率。
锂离子电池及其负极材料以及该负极材料的制备方法.pdf
本发明提供了一种锂离子电池及其负极材料以及该负极材料的制备方法,通过该方法制备的负极材料,所述负极材料由碳化的动物毛发制成,将动物毛发进行粉碎;将得到的粉碎后的动物毛发放入加热炉中碳化,加热温度为700‑1100℃,加热时间为3‑5小时,解决了现有石墨材料作为锂离子电池负极材料充放电比容量低,充放电性能差的问题。