
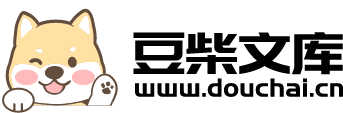
一种分级喷氨烟气脱硝装置及方法.pdf
哲妍****彩妍
在线预览结束,喜欢就下载吧,查找使用更方便
相关资料
一种分级喷氨烟气脱硝装置及方法.pdf
本发明提出一种分级喷氨烟气脱硝装置和方法,包括第一级喷氨格栅,第一级催化剂层,第一级混合器,第二级混合器,第二级喷氨格栅,整流器,第二级第一催化剂层,第二级第二催化剂层,第二级备用催化剂层,第一级控制阀,第二级控制阀和还原剂流量控制总阀,所述装置与锅炉尾部烟道连接,设置两级脱销装置,可以在现有的技术条件下,达到高的脱硝效率及低的氨逃逸量。
一种烟气脱硝系统喷氨调节装置.pdf
本发明公开了一种烟气脱硝系统喷氨调节装置,包括锅炉、喷氨调节装置、氨水罐和反应器,锅炉的烟气出口通过烟道连接反应器的烟气进口,喷氨调节装置包括多个喷氨机构、多块下档板和多块上挡板,多块下档板的底端等间隔固定于烟道的底壁上,多块上挡板的顶端等间隔固定于烟道的顶壁上,且上挡板位于相邻两个下挡板之间的中部,喷氨机构设置于相邻上挡板和下档板之间,包括喷氨总管,喷氨总管的两侧均连接有多个等间隔分布的喷氨支管。本发明可增加烟气与氨之间的混合时间,使得二者混合的更加充分,降低氨逃逸,提高脱硝效率。
脱硝烟气量确定方法、装置及脱硝喷氨量调整方法、装置.pdf
本发明涉及脱硝烟气量确定方法、装置及脱硝喷氨量调整方法、装置,脱硝烟气量确定方法包括获取SCR脱硝系统中A、B两侧SCR脱硝反应器的烟道压差△PA、△PB;根据△PA、△PB,计算得到KA以及KB;获取锅炉设计BMCR工况烟气量、当前锅炉总风量、锅炉设计总风量以及漏风修正系数;根据KA、KB、锅炉设计BMCR工况烟气量、当前锅炉总风量、锅炉设计总风量以及漏风修正系数,计算得到A侧脱硝烟气量以及B侧脱硝烟气量,本发明提供的脱硝烟气量确定方法能够得到准确的脱硝烟气量,从而对喷氨量进行更为合理的调节,达到控制单
一种用于烟气脱硝的喷氨流量调节装置.pdf
本实用新型公开了一种用于烟气脱硝的喷氨流量调节装置,属于脱硝辅助设备技术领域。它包括喷氨管路和安装在喷氨管路上的多组喷嘴,所述喷嘴包括外壳、滑套、弹簧和喷管,所述滑套与外壳的内壁滑动套接,所述弹簧设置在滑套和外壳之间,所述喷管与滑套的内壁转动套接,所述喷管上开设有通槽,所述通槽延伸至外壳外,实现喷嘴流量调节。本实用新型通过喷管的滑动设置,该结构可根据管路内、外压力的变化,对通槽的开度做出实时的调整,从而调节了喷嘴流量,使喷嘴的流量与压力适配,在喷氨管路压力基本均匀情况下,而实现喷嘴气流的均匀分配。
用于SCR脱硝装置的高温喷氨装置及喷氨方法.pdf
本发明涉及一种用于SCR脱硝装置的高温喷氨装置及喷氨方法。燃料燃烧过程中产生的氨氧化物已成为主要的大气污染物,其过量排放会引发酸雨、光化学烟雾。臭氧层破坏等一系列环境问题,因此控制和治理氨氧化物污染非常有必要性。一种用于SCR脱硝装置的高温喷氨装置,其组成包括:喷射母管(1),所述的喷射母管上具有一组喷射支管(2),所述的喷射支管上安装有氨气喷嘴(3),所述的喷射母管的左端上具有氨气流量调节阀(4)。本发明应用于SCR脱硝装置的高温喷氨装置及喷氨方法。