
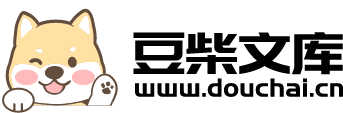
一种掺杂畜禽粪便的污泥基生物炭的制备方法.pdf
猫巷****志敏
在线预览结束,喜欢就下载吧,查找使用更方便
相关资料
一种掺杂畜禽粪便的污泥基生物炭的制备方法.pdf
本发明涉及一种掺杂畜禽粪便的污泥基生物炭制备方法。其方法是:将市政污泥和畜禽粪便分别风干,放入烘箱于105℃烘到恒重,破碎至4‑8mm;将市政污泥和畜禽粪便充分混合,研磨,过200目筛;将物料置入气氛马弗炉中热解,冷却得到热解产物;将热解产物用盐酸浸洗,用去离子水浸泡20min后过滤,重复5遍,再把滤上物放入烘箱于105℃烘干至恒重,获得掺杂畜禽粪便的污泥基生物炭。本发明节约制备成本,克服了生物炭制备的局限性,使得污泥和畜禽粪便变废为宝,同时很大程度上提高污泥基生物炭的品质与污水处理性能。
一种掺杂毛发的污泥基生物炭的制备方法.pdf
本发明涉及一种掺杂毛发的污泥基生物炭的制备方法。其方法是:1、市政污泥风干后放入烘箱到恒重,破碎、研磨、过200目筛;毛发经研磨、过筛成200目的粉末。2、将污泥与毛发按照重量份1~3:1的比例混合。3、将混合物置入气氛马弗炉中热解,通入氮气后升温加热至400‑600℃,停留2‑3h后,降温至80℃出料,冷却得热解产物。4、将步骤3)产物用盐酸浸洗5min,去离子水浸泡后过滤,重复5遍,再把滤上物放入烘箱烘干至恒重,获得掺杂毛发的污泥基生物炭。本发明节约了污泥基生物炭的制备成本,克服了污泥基生物炭制备的
一种掺杂菌糠的污泥基生物炭的制备方法.pdf
本发明涉及环境修复材料研发与应用领域,公开了一种掺杂菌糠的污泥基生物炭的制备方法,工艺步骤为:分别将污泥和菌糠自然风干;将风干后的污泥和菌糠分别放入粉碎机中粉碎后过60目筛;将污泥和菌糠混合均匀;将污泥和菌糠按一定的原料配比放入马弗炉中,在一定的温度条件下热解一定的时间,得到污泥‑菌糠复合生物炭。本发明生物炭的产率为51~60%,亚甲基蓝吸附值为18~25mg/g,吸附率为61~84%。以城市污水处理厂的脱水污泥和食用菌生产废料香菇菌糠这两种固体废弃物为原料,采用限氧热解技术,开发污泥‑菌糠复合生物炭吸附
一种畜禽粪便制备生物炭的制备方法.pdf
本发明公开了一种畜禽粪便制备生物炭的制备方法,包括以下步骤,步骤一,根据畜禽粪便的含水率加入干化料并进行搅拌形成混合料,直至混合料的含水率≤45%;步骤二,将混合均匀的混合料直接送入厌氧热解内热式炭化炉进行炭化并生成生物炭,炭化温度为450‑700℃。该畜禽粪便制备生物炭的制备方法准备生物炭的投入少,产出效益高,同时对畜禽粪便进行了无害化处理并生成生物炭,可安全健康返田,并且出炭率高,生物炭品质较好。
一种掺杂甲壳的污泥基生物炭的制备方法.pdf
本发明涉及一种污泥基生物炭,特别是涉及一种掺杂甲壳的污泥基生物炭制备方法。通过如下实现:市政污泥风干后放入烘箱于105℃烘到恒重,破碎至4‑8mm。用无水乙醇,在60℃条件下对甲壳进行30min脱脂,余下放入烘箱于105℃烘干,破碎至5~8mm。按1~3:1重量份比例将市政污泥和甲壳充分混合研磨,过200目筛;将物料置入气氛马弗炉中,通入氮气,升温速度加热得到热解产物。将热解产物用1‑3M的盐酸浸洗5min,重复5遍,再把滤上物放入烘箱于105℃烘干至恒重,最终获得掺杂甲壳的污泥基生物炭。本发明节约了制备