
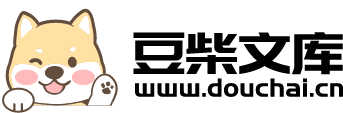
一种减少单晶叶片平台疏松缺陷的工艺方法.pdf
春景****23
在线预览结束,喜欢就下载吧,查找使用更方便
相关资料
一种减少单晶叶片平台疏松缺陷的工艺方法.pdf
本发明的目的在于提供一种减少单晶叶片平台疏松缺陷的工艺方法,其特征在于:将叶片平台高处位置置于靠近模壳中心的位置,平台低处位置靠近定向凝固炉的炉壁处,利用横向梯度降低方向与枝晶间补缩方向相反的原理,平台高处先凝固,保证其枝晶间得到叶身处合金液的补缩,从而避免高处平台产生表面凝固疏松,以提高单晶叶片质量。
一种减少单晶叶片平台处杂晶缺陷的装置及其方法.pdf
本发明提供了一种减少单晶叶片平台处杂晶缺陷的装置,包括水冷盘和设置于水冷盘上方的叶片模壳以及模壳中柱;所述叶片模壳上设置有叶片平台,所述叶片平台沿远离模壳中柱的一侧向靠近模壳中柱的一侧方向由高到低倾斜设置,且所述叶片平台的低处一侧与模壳中柱之间设置有反射层挡板,所述反射层挡板与所述叶片平台之间留有间隙;其可减少叶片平台尖端处的杂晶及疏松等缺陷,且不增加工艺操作难度,不改变原有模壳结构,也不增加额外热源或引晶条,结构简单,操作简便,大大降低制造成本。
单晶叶片自由表面消除疏松的工艺方法.pdf
单晶叶片自由表面消除疏松的工艺方法,其特征在于:首先制备涡轮叶片蜡模,缘板自由表面带补缩带,经涂料制壳、脱蜡、定向凝固、脱壳清理、脱芯、磨削掉补缩带,最后得到无表面疏松的单晶涡轮叶片。本发明通过与叶片自由表面随型的“井”式补缩带对叶片缘板自由表面进行充分补缩,见图1与图2,有效消除其表面的显微疏松,提高单晶叶片的合格率。
一种降低单晶高温合金叶片榫头内部疏松缺陷形成的方法.pdf
本发明涉及高温合金单晶叶片制备技术领域,具体为一种降低单晶高温合金叶片榫头内部疏松缺陷形成的方法。该方法步骤如下:(1)单晶高温合金引晶条模具设计时,确保引晶条的尺寸与叶片榫头尺寸相适应;(2)在工装模具上将引晶条与单晶高温合金叶片榫头相连接;(3)将单晶高温合金叶片蜡型进行挂浆、淋砂,脱蜡后烧结制成刚玉模壳;(4)将刚玉模壳置于定向凝固炉中进行凝固,制备单晶高温合金叶片。本发明利用竞争生长的思想,将叶身上的树枝晶引入厚大的榫头部分,利用引晶条所引入树枝晶与榫头处树枝晶之间的竞争生长与自适应调节,使单晶高
一种单晶叶片的制造工艺及其测试方法.pdf
本发明属于合金铸造应用技术领域,具体公开了单晶叶片的制造工艺,包括以下步骤,步骤1、制作模壳。步骤2、模壳烧制。步骤3、过滤器的安装。步骤4、将模壳安装到熔炉中。步骤5、铸造工艺在ALD的Bridgman炉中进行。步骤6、铸造后,得到单晶涡轮叶;测试方法,包括以下步骤,步骤a、水刀切割后,蚀刻表面;步骤b、观察涡轮机叶片,在启动器中可看到许多定向凝固的晶粒,这意味着涡轮机叶片由单晶组成。本发明的有益效果在于:其通过Bridgman方法可制备出符合使用标准要求的单晶镍基高温合金叶片,同时可对单晶镍基高温合金