
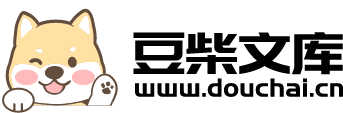
氮化硅沉积炉管及其自动去膜工艺流程优化的方法.pdf
依波****bc
亲,该文档总共12页,到这已经超出免费预览范围,如果喜欢就直接下载吧~
相关资料
氮化硅沉积炉管及其自动去膜工艺流程优化的方法.pdf
本发明属于半导体存储器组件领域,具体为氮化硅沉积炉管及其自动去膜工艺流程优化的方法。一种氮化硅沉积炉管,包括外石英管和内石英管,所述内石英管设置于所述外石英管内部,所述内石英管内部还设置有晶舟,所述晶舟下方设有晶舟载台,所述晶舟载台的下方设有载盘遮护垫,所述载盘遮护垫边缘设置有环形遮护部,所述环形遮护部的外径与所述载盘遮护垫的直径为对应匹配所述晶舟底端设有底座套环,所述底座套环套于所述晶舟载台上。本发明通过改进现有氮化硅沉积炉管硬件设施,避免了晶舟载台金属物质与腐蚀气体产生化学反应产生黑色微尘颗粒,进而避
一种LPCVD炉管自动调控沉积膜厚的方法.pdf
一种LPCVD炉管自动调控沉积膜厚的方法,包括:提供LPCVD炉管,并设置热电偶及监控片,且各监控片将放置区划分为各控制区域;在各控制区域填充未图案化晶圆,进行对应制程测试运行;量测各监控片之沉积膜厚,并反馈至调控系统;调控系统根据量测厚度与目标厚度的差异执行作业时间和温度的调节,并作为基准时间温度;跑货时将Lot数目、位置,晶圆数量、图案化密度发送至调控系统,计算获得各区域平均图案化密度,进而计算获得各监控片需补偿的厚度;调控系统根据补偿厚度计算出需要补偿的时间与温度,在基准时间与温度的基础上进一步计算
炉管设备及其沉积方法.pdf
一种炉管设备及其沉积方法,所述炉管设备包括:炉管腔体;用于放置晶圆的晶圆基座,位于所述炉管腔体内;多组进气管路,与所述炉管腔体连通,所述多组进气管路分时开启,每组进气管路在开启时向所述炉管腔体输入相应的一组待反应物,其中,不同组的待反应物用于生成不同类别的生成物;出气管路,与所述炉管腔体连通,所述炉管腔体内的反应后气体经由所述出气管路输出。本发明方案可以在同一个炉管腔体中分时地形成多种介质层,有助于降低耗时并提高产能,提高产品质量和良率。
沉积炉管内管、沉积炉管以及沉积方法.pdf
本发明提供了一种沉积炉管内管,内管管壁内具有至少一个气体流通区,气体流通区对应的管壁包括内壁和外壁;内壁不同相对高度上设置有若干层排气孔,使得气体流通区中的气体能通过排气孔进入沉积区中;一个高度层中的排气孔的总流通面积随其相对高度的升高而增大,使得单位时间内,不同高度层的排气孔的排气均匀;外壁或管壁的底部设置有与气体流通区连通的进气口。本发明还提供了一种包括上述内管的沉积炉管和使用这种炉管进行沉积的沉积方法。本发明提供的沉积炉管内管、沉积炉管和沉积方法能够改善晶圆上沉积膜厚度的均匀性。
PECVD沉积氮化硅膜的工艺研究.docx
PECVD沉积氮化硅膜的工艺研究摘要:PECVD(PlasmaEnhancedChemicalVaporDeposition)是一种常用的沉积薄膜的工艺方法。本文主要研究PECVD沉积氮化硅膜的工艺,探讨了工艺参数对膜品质的影响,总结了优化的工艺条件。实验结果表明,通过调节沉积气体比例、功率密度和沉积时间等参数,能够得到高质量的氮化硅膜。本研究对今后在半导体工艺中应用PECVD沉积氮化硅膜具有一定的借鉴意义。关键词:PECVD,氮化硅膜,工艺参数,膜品质,优化条件1.引言在现代电子器件中,薄膜材料的应用越