
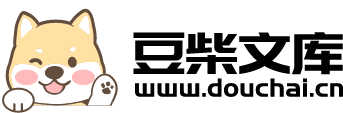
利用硫酸铝铵浓缩钛白废酸的方法.pdf
一吃****仪凡
在线预览结束,喜欢就下载吧,查找使用更方便
相关资料
利用硫酸铝铵浓缩钛白废酸的方法.pdf
本发明公开了一种利用硫酸铝铵浓缩钛白废酸的方法,属于化学领域,包括以下步骤:将钛白废酸与硫酸铝铵分别置于同一密闭容器中,待浓缩完成后,即得质量百分浓度为50~55%的硫酸。本发明方法完全避免了锅炉及蒸发器的使用,避免了昂贵的耐腐蚀材料的使用,从而降低生产成本,而且操作均在常温下或稍加热的条件下进行,这样极大地改善了工作条件,也使得钛白废酸浓缩的经济性得到提高。
利用硫酸铝钾浓缩钛白废酸的方法.pdf
本发明公开了一种利用硫酸铝钾浓缩钛白废酸的方法,属于化学领域,包括以下步骤:将钛白废酸与硫酸铝钾分别置于同一密闭容器中,待浓缩完成后,即得质量百分浓度为50~55%的硫酸。本发明方法完全避免了锅炉及蒸发器的使用,避免了昂贵的耐腐蚀材料的使用,从而降低生产成本,而且操作均在常温下或稍加热的条件下进行,这样极大地改善了工作条件,也使得钛白废酸浓缩的经济性得到提高。
利用偏硼酸钙浓缩钛白废酸的方法.pdf
本发明公开了一种利用偏硼酸钙浓缩钛白废酸的方法,属于化学领域,包括以下步骤:将钛白废酸与偏硼酸钙分别置于同一密闭容器中,待浓缩完成后,即得质量百分浓度为50~55%的硫酸。本发明方法完全避免了锅炉及蒸发器的使用,避免了昂贵的耐腐蚀材料的使用,从而降低生产成本,而且操作均在常温下或稍加热的条件下进行,这样极大地改善了工作条件,也使得钛白废酸浓缩的经济性得到提高。
利用四硼酸钠浓缩钛白废酸的方法.pdf
本发明公开了一种利用四硼酸钠浓缩钛白废酸的方法,属于化学领域,包括以下步骤:将钛白废酸与四硼酸钠分别置于同一密闭容器中,待浓缩完成后,即得质量百分浓度为50~55%的硫酸。本发明方法完全避免了锅炉及蒸发器的使用,避免了昂贵的耐腐蚀材料的使用,从而降低生产成本,而且操作均在常温下或稍加热的条件下进行,这样极大地改善了工作条件,也使得钛白废酸浓缩的经济性得到提高。
利用三氯化铁浓缩钛白废酸的方法.pdf
本发明公开了一种利用三氯化铁浓缩钛白废酸的方法,属于化学领域,包括以下步骤:将钛白废酸与三氯化铁分别置于同一密闭容器中,待浓缩完成后,即得质量百分浓度为50~55%的硫酸。本发明方法完全避免了锅炉及蒸发器的使用,避免了昂贵的耐腐蚀材料的使用,从而降低生产成本,而且操作均在常温下或稍加热的条件下进行,这样极大地改善了工作条件,也使得钛白废酸浓缩的经济性得到提高。