
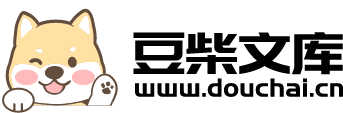
一种从高炉布袋灰中回收钾、钠、锌的工艺方法.pdf
Jo****63
在线预览结束,喜欢就下载吧,查找使用更方便
相关资料
一种从高炉布袋灰中回收钾、钠、锌的工艺方法.pdf
本发明涉及一种从高炉布袋灰中回收钾、钠、锌的工艺方法,其原料是高炉布袋灰,目的是实现钾、钠、锌的回收和含铁渣在钢厂内的循环利用。该方法包括水洗回收钾钠工艺、还原挥发锌工艺及湿法回收锌工艺。具体的:高炉布袋灰经水洗后得到含氯化钾和氯化钠的滤液,氯化钾或氯化钠溶解度饱和的滤液经净化、分步结晶制得KCl和NaCl产品;氯化钾或氯化钠溶解度不饱和的滤液继续返回水洗步骤,水洗渣烘干后与还原剂和粘结剂按一定的质量比混匀制粒,之后在还原设备中进行锌的高温还原挥发,含铁渣在钢厂内循环利用;烟气回收系统中回收的富锌粉尘经湿
回收高炉布袋灰中锌、铟、铅的方法.pdf
本发明属于冶金技术领域,具体涉及回收高炉布袋灰中锌、铟、铅的方法。本发明解决的技术问题是提供回收高炉布袋灰中锌、铟、铅的方法。该回收方法包括以下步骤:将高炉布袋灰加水配成浆料,向浆料中边加入十二烷基苯磺酸钠浮选剂溶液边搅拌,并将产生的泡沫刮出,然后将泡沫过滤、干燥后,得富集料。本发明通过浮选法来富集和回收高炉布袋灰中锌、铟、铅,进一步地结合高温还原挥发来富集和回收高炉布袋灰中锌、铟、铅。得到的最终产物中锌、铟、铅的富集效果更好、品位更高。
高炉布袋灰中锌、铟、铅的回收方法.pdf
本发明属于冶金技术领域,具体涉及高炉布袋灰中锌、铟、铅的回收方法。本发明解决的技术问题是提供高炉布袋灰中锌、铟、铅的回收方法。该回收方法包括以下步骤:将高炉布袋灰加水配成浆料,将浆料通过旋流分级得到溢流轻相浆料和底流重相浆料,然后将溢流轻相浆料浓缩、沉降、过滤后干燥,即得到富集料。进一步地,将富集料与煤粉混合后经高温还原挥发,收集挥发烟尘,即得主要含锌、铟、铅的回收产物。该回收方法综合回收高炉布袋灰中的有价元素锌、铟、铅,提高固废资源的综合利用率和综合经济价值。
一种回收高炉瓦斯灰中锌的方法.pdf
一种回收高炉瓦斯灰中锌的方法,本发明首先将瓦斯灰在亚氨基二乙酸‑硫酸铵‑氨水组成的浸出体系中进行配位浸出,使大部分锌进入溶液中,并抑制铁的溶解,实现瓦斯灰中锌与铁的分离;对于含锌浸出液,进行蒸氨和氨气的吸收,所得氨水返回浸出过程重复利用;蒸氨后液通过加入稀硫酸调节溶液pH,使浸出液中的亚氨基二乙酸重结晶析出,过滤所得析出后液为硫酸锌溶液,可与传统的溶剂萃取‑电积回收锌工序衔接。本发明不但避免了强酸性体系对浸出设备的腐蚀,也避免了强碱性体系中生成的锌酸钠难以回收问题。锌的浸出率为65%以上,而铁几乎没有被浸
一种高炉布袋灰资源化利用工艺方法.pdf
本申请公开了一种高炉布袋灰资源化利用工艺方法,其原料是高炉布袋灰,目的是实现氯、钾、锌的资源化回收以及含铁、碳物料在钢厂的内循环利用。所述工艺方法包括高炉布袋灰药剂水洗分步结晶回收钾钠工艺步骤、氨‑铵盐浸出氧化锌工艺步骤及蒸发结晶煅烧回收氧化锌工艺步骤。本发明的工艺流程实现了高炉布袋灰的高值化利用和其在钢厂内的循环利用,促进钢铁企业节能减排、变废为宝。