
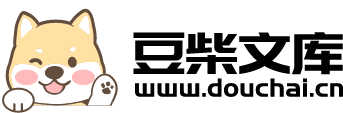
精确控制渗碳层深度的热处理工艺.pdf
书生****12
在线预览结束,喜欢就下载吧,查找使用更方便
相关资料
精确控制渗碳层深度的热处理工艺.pdf
本发明提供一种精确控制渗碳层深度的热处理工艺,包括如下步骤:步骤一:进炉;步骤二:均温加热;步骤三:在低温下强渗;步骤四:在降温过程中进行扩散;步骤五:淬火;步骤六:回火。本发明的有益效果是:本发明解决了常规渗碳淬火工艺不能解决的窄范围渗碳层深度控制问题。降温过程替代扩散过程。
渗碳层马氏体微裂纹与热处理工艺.docx
渗碳层马氏体微裂纹与热处理工艺渗碳层马氏体微裂纹与热处理工艺摘要渗碳层马氏体微裂纹是一种常见的表面裂纹缺陷,会对渗碳件的性能和使用寿命造成不利影响。本文主要研究了渗碳层马氏体微裂纹的形成机理和热处理工艺对其的影响。实验结果表明,热处理工艺能够有效减少马氏体微裂纹的发生,并提高渗碳层的质量和性能。因此,合理选择和优化热处理工艺是预防渗碳层马氏体微裂纹的关键。关键词:渗碳层,马氏体微裂纹,热处理工艺引言渗碳是一种常用的表面强化处理方法,其能显著提高金属材料的硬度和耐磨性能。然而,渗碳层马氏体微裂纹是渗碳层中常
控制渗碳层质量的新工艺.docx
控制渗碳层质量的新工艺控制渗碳层质量的新工艺摘要随着工业技术的发展,渗碳工艺在金属加工领域扮演着重要的角色。本论文研究了一种新的渗碳工艺,旨在控制渗碳层的质量。通过合理调控温度、时间和气氛等工艺参数,以及改良传统工艺的问题,可以有效提高渗碳层的质量,提高金属材料的硬度和耐腐蚀性。本文将详细介绍新工艺的原理、步骤和实验结果,并对其优点和应用前景进行讨论。1.引言渗碳是一种通过碳在金属表面形成固溶体的过程。渗碳工艺常用于提高金属材料的硬度、耐磨性和耐腐蚀性。然而,在传统的渗碳工艺中,往往存在渗碳层质量不稳定、
齿轮渗碳层深度超标返修工艺探讨.docx
齿轮渗碳层深度超标返修工艺探讨齿轮渗碳层深度超标返修工艺探讨摘要:齿轮渗碳层深度超标是一种常见的加工缺陷,这种情况会导致齿轮的使用寿命大大缩短。本文论述了齿轮渗碳层深度超标的原因和影响,并提出了一种有效的返修工艺,以确保渗碳层的符合要求。关键词:齿轮,渗碳,深度超标,返修工艺1.引言齿轮是传动装置中最常见的零件之一,其质量直接影响到整个机械系统的性能和可靠性。渗碳是一种提高齿轮硬度和耐磨性的常用工艺,但在实际生产中,齿轮渗碳层深度超标的情况时有发生,这会导致齿轮的寿命大大缩短,甚至导致设备故障。2.渗碳层
无过共析层的渗碳工艺.docx
无过共析层的渗碳工艺无过共析层的渗碳工艺摘要:无过共析层的渗碳工艺是一种新型的表面处理技术,可以显著提高金属材料的表面硬度、耐磨性和抗腐蚀性能。本文主要介绍了无过共析层的渗碳工艺原理、工艺流程和影响因素,并对其应用前景进行了展望。关键词:无过共析层、渗碳、工艺流程、应用前景引言:金属材料的表面性能对于其在各个领域的应用都起着至关重要的作用。而传统的渗碳工艺虽然能够提高金属材料的硬度和耐磨性,但存在共析层的问题,导致表面性能的不稳定和脆化现象。为了解决这个问题,研究人员提出了无过共析层的渗碳工艺,该工艺不仅