
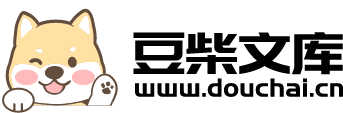
一种基于冲击回波法的高炉炉衬监测方法.pdf
王秋****哥哥
在线预览结束,喜欢就下载吧,查找使用更方便
相关资料
一种基于冲击回波法的高炉炉衬监测方法.pdf
本发明提供一种基于冲击回波法的高炉炉衬监测方法,采用第一系统和第二系统实现,所述的第一系统为需要在高炉炉体植入固定侵入式传感器的炉衬监测系统,所述固定侵入式传感器为热电偶或能够与炉衬等效损耗的传感器,所述的第二系统为基于冲击回波法的单点或扫描式可移动监测系统。充分利用并结合现有常规固定侵入式炉衬监测系统,通过联合运用、扬长避短,将常规监测系统的高准确度与冲击回波法的高灵活性密切结合,有效提高冲击回波系统对高炉监测的准确度,同时有效增加高炉炉衬监测区域范围,减少或避免了监测死角和盲区,为更加全方位且精确快捷
基于冲击回波法的高炉炉衬厚度检测方法.docx
基于冲击回波法的高炉炉衬厚度检测方法摘要本文研究了基于冲击回波法的高炉炉衬厚度检测方法,该方法通过发送超声波脉冲,测量回波信号的时间和强度来确定高炉炉衬的厚度。通过对此方法的原理和特点进行分析得出,该方法具有非接触、快速、准确等优点。本文对该方法的应用进行了介绍,并分析了该方法在高炉炉衬厚度检测中的应用前景。关键词:冲击回波法;高炉炉衬厚度检测;超声波脉冲;回波信号AbstractThispaperstudiesthemethodofdetectingthethicknessofblastfurnacel
一种对高炉炉衬冲击回波检测的信号处理方法及系统.pdf
本发明公开了一种对高炉炉衬冲击回波检测的信号处理方法及系统,通过利用时差超声法对被测对象的材料做波速标定,获得标定波速信息,对冲击回波信号进行经验模态分解,获得本征模态分量,基于本征模态分量,对冲击回波信号进行滤波,获得滤波信号以及基于滤波信号的能量算子,对滤波信号进行分类,并基于分类结果和波速信息获得高炉炉衬最内层的厚度信息,解决了现有技术由于弹性波在非均匀分层介质中传播产生的混叠效应,导致对高炉炉衬侵蚀状态检测结果偏差大的技术问题,通过对采集的冲击回波信号去噪以及进一步采用能量算子对滤波信号分类,能有
基于冲击回波法的箱梁厚度检测方法研究.docx
基于冲击回波法的箱梁厚度检测方法研究为题目,写不少于1200的论文AbstractThedetectionofthicknessofboxbeamsisacrucialtechniqueforensuringthestructuralintegrityofbridgesandotherinfrastructure.Inthisstudy,weproposeanovelnon-destructivetestingmethodformeasuringthethicknessofboxbeamsusingthe
高炉炉衬烧蚀监测装置及其监测方法.pdf
本发明公开高炉炉衬烧蚀监测装置,包括炉体、电阻监测机构、冲击弹性波监测机构和智能控制器,通过多个电阻监测机构、多个冲击弹性波监测机构和智能控制器的相互配合,可以实现多点进行监测工作,而多个电阻监测机构可以完成电阻法监测工作,从而就可以完成对烧蚀后的炉衬的厚度监测工作,多个冲击弹性波监测机构可以完成炉衬的早期缺陷的监测工作以及可以对烧蚀的高炉炉衬进行监测工作,这样就可以提高监测精度,也不会耽误抢修时机;通过第一接近开关、第二接近开关与两个接近块的相互配合,能同时完成FMT传感器和弹性波接收器的控制工作,从而