
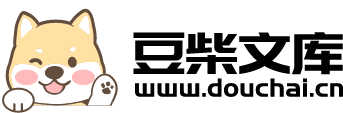
一种增材制造用铜包覆钨球形复合粉末的制备方法.pdf
是立****92
在线预览结束,喜欢就下载吧,查找使用更方便
相关资料
一种增材制造用铜包覆钨球形复合粉末的制备方法.pdf
本发明提供了一种增材制造用铜包覆钨球形复合粉末的制备方法,包括以下步骤:(1)将可溶硝酸铜类粉末溶于无水乙醇或去离子水中,用机械搅拌和超声处理使其充分溶解;然后加入球形钨粉末,再次用机械搅拌和超声处理使球形钨粉末完全润湿;(2)将固液混合物置于干燥箱中,完全干燥后得到复合粉末;(3)将复合粉末置于管式炉中,还原性气氛高温煅烧;冷却至室温,得到铜包覆钨球形复合粉末;(4)将铜包覆钨球形复合粉末从管式炉中取出,研磨至无块状颗粒。本发明能够使不同配比的铜完整且均匀地包覆在金属颗粒表面,在制备方法过程中保持了金属
一种制备增材制造用金属球形粉末的方法.pdf
本发明公开了一种制备增材制造用金属球形粉末的方法,包括:按照金属球形粉末所需成分进行配料;将配好的料置于熔炼炉中;将熔炼炉抽真空到预设真空度时进行熔炼,并在熔炼过程中充入氮气保护,获得金属溶液;将金属溶液升温至熔点以上预设过热度,并在高压雾化介质作用下,对金属溶液进行雾化,获得雾化粉末;对雾化粉末进行冷却,获得金属球形粉末。采用本实施例中的方法所制备的增材制造用金属球形粉末,具有球形度高、氧含量低的优点。
一种增材制造用球形金属粉末的制备方法.pdf
本发明涉及合金粉末制造技术领域,尤其涉及一种增材制造用球形金属粉末的制备方法,包括如下步骤:S1、将生母合金放入熔炼炉中,进行抽真空,待感应熔炼炉中合金融化,关闭抽真空系统,通入惰性气体,对合金进行熔炼,熔炼过程中通入惰性保护气体,第一次熔炼之后,进行第二次熔炼;S2、将熔融的金属液放入中间包中,启动惰性气体加热装置,加热雾化气体;S3、通过导流管将金属熔液引入改进后的紧耦合真空气雾化设备,液体飞行过程中凝固成球形粉末颗粒;S4、通过滤压进行水粉分离,然后干燥,气流分级,得到3D打印金属粉体。采用VIGA
一种铜包覆铬复合粉末的制备方法.pdf
本发明公开了粉末冶金技术领域的一种铜包覆铬复合粉末的制备方法。该制备方法将草酸铜粉末、超细铜粉、铬粉和粘结剂按照一定顺序充分混合后,置于氢气还原炉中高温处理,经冷却、破碎、筛分即可得到目标细度的铜包覆铬复合粉末;利用本发明制备方法制备得到的铜包覆铬复合粉末包覆率高、包覆层厚、铜含量高、无成分偏析,具有工艺流程短,环境友好,生产成本低的优点,易于工业化推广。
一种增材制造覆铜石墨烯/铝合金复合材料的制备方法.pdf
本发明公开了一种增材制造覆铜石墨烯/铝合金复合材料的制备方法,包括:S1、对石墨烯片层进行表面金属化处理;S2、将得到表面均匀覆铜的石墨烯片层与铝合金粉末进行湿法低能球磨;S3、过滤、晾干、烘干后进行短时低能干磨,筛粉,得到覆铜石墨烯/铝合金复合粉末;S4、采用增材制造工艺直接成型高致密的覆铜石墨烯/铝合金复合材料。本发明通过先采用化学法对石墨烯片层进行表面金属化处理,接着采用湿法低能球磨工艺得到复合粉末,最后通过增材制造技术制备得到石墨烯分布均匀、界面结合良好,且具有优异的热学以及力学性能的覆铜石墨烯/