
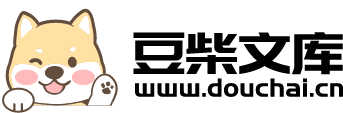
一种薄壁变壁厚变截面双向深腔类构件多向锻造成形方法.pdf
一吃****书竹
亲,该文档总共11页,到这已经超出免费预览范围,如果喜欢就直接下载吧~
相关资料
一种薄壁变壁厚变截面双向深腔类构件多向锻造成形方法.pdf
本发明公开一种薄壁变壁厚变截面双向深腔类构件多向锻造成形方法,包括步骤,切割圆饼状的坯料,并进行去除表面氧化皮的预处理;将预处理过的坯料加热至100℃~150℃后,在坯料表面均匀涂抹石墨水溶液,再放入加热炉中继续加热至420℃~480℃,保温90分钟;将多向锻造模具加热至180℃~230℃,并将坯料放置于成型腔体内进行多向锻造成形,多向锻造模具采用上模和下模的上下分模方式,左侧侧缸带动的左冲头和/或右侧侧缸带动的右冲头分别往中心运动,锻造完成;本发明通过工艺改进采用多向锻造方法一步成形出锻件,该方法采用圆
厚壁变截面刚架的内力分析.docx
厚壁变截面刚架的内力分析厚壁变截面刚架是一种结构形式,在工程中应用广泛。它由多个柱段和梁段组成,柱段和梁段的截面尺寸随着高度的变化而变化。这种结构形式具有较好的变形和刚度特性,因此在大跨度和高层建筑中得到了广泛的应用。在本文中,我们将对厚壁变截面刚架进行内力分析,以了解其工作原理和性能。厚壁变截面刚架的内力分析需要考虑以下几个方面:荷载的作用、结构的变形和刚度特性、构件的受力状况。首先,我们需要根据实际工程需求确定荷载类型和作用位置。常见的荷载包括自重、活载、风载等。这些荷载可以通过结构分析的方法求解每个
变截面异形薄壁结构件激光内送粉熔覆成形研究.docx
变截面异形薄壁结构件激光内送粉熔覆成形研究标题:变截面异形薄壁结构件激光内送粉熔覆成形研究摘要:随着制造业的发展,对于高性能异形薄壁结构件的需求逐渐增加。然而,传统的制造方法在生产此类零件时面临着诸多挑战,如形状复杂问题、工艺复杂度高等。本论文以激光内送粉熔覆成形技术为基础,研究了如何有效实现变截面异形薄壁结构件的生产,并针对其制造过程中可能出现的问题进行了分析和优化。引言:变截面异形薄壁结构件具有复杂的三维形态和高精度要求,传统的制造方法无法满足其生产需求。激光内送粉熔覆成形技术作为一种高效且精度较高的
异型变截面管材内高压成形壁厚控制技术与材料流动规律研究.docx
异型变截面管材内高压成形壁厚控制技术与材料流动规律研究引言随着工业现代化和科技的进步,异型变截面管材的应用范围越来越广。一些高端石油管道、天然气管道、化工管道等都采用了异型变截面管材,以提高其承载能力和抗外力能力。然而,在异型变截面管材的加工过程中,存在一些难以控制的因素,例如管材的壁厚控制和材料流动规律,这些因素会严重影响到管材的质量、使用寿命以及管道系统的运行安全。因此,本文旨在研究异型变截面管材内高压成形壁厚控制技术及材料流动规律,为异型变截面管材的生产和应用提供一些参考。一、异型变截面管材高压成形
一种复杂薄壁构件蠕变时效成形屈曲抑制装置及方法.pdf
本发明公开了一种复杂薄壁构件蠕变时效成形屈曲抑制装置及方法,其中装置包括两个底座、两根螺杆、横梁以及若干个恒力加载单元,两个底座分别设置在成形工装的两侧、两根螺杆分别与两个底座相连,横梁的两端分别与两根螺杆相连,若干个恒力加载单元安装在横梁上;通过将所有恒力加载单元的轴线均与待成形坯料屈曲区的法向重合,顶杆对坯料屈曲区域施加恒力,实现在蠕变时效成形过程中对坯料屈曲区域的约束,有效抑制复杂薄壁构件蠕变时效成形过程中的屈曲。同时,本发明方法的复杂薄壁构件蠕变时效成形屈曲抑制方法,提高了成形精度,增大了构件成功