
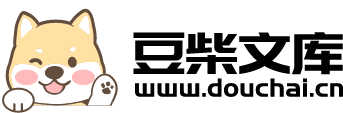
一种多热源耦合熔融装置及方法.pdf
是你****盟主
在线预览结束,喜欢就下载吧,查找使用更方便
相关资料
一种多热源耦合熔融装置及方法.pdf
本发明公开了一种用于固废处理的多热源耦合熔融装置及方法。一种多热源耦合熔融装置,装置的上部为气化室,中部为燃烧室,下部为熔融池;气化室和熔融池呈圆柱状;气化室顶部设有排气口;气化室外侧面设有进料螺旋;气化室底部设有炉排;燃烧室内设置燃烧机和等离子炬;熔融池底部设有加热电极和出料口。一种多热源耦合熔融处理方法,采用上述多热源耦合熔融装置处理固废。本发明的多热源耦合熔融装置采用等离子炬、电极、燃烧机协同加热,有利于改善装置运行的稳定性,改善装置内部温度分布,提高熔融效率和系统稳定性,减少壁面腐蚀,提高产能,显
一种多热源耦合加热块矿的烘干装置及烘干方法.pdf
本发明涉及高炉精料技术领域,具体涉及一种多热源耦合加热块矿的烘干装置及烘干方法。本发明提供的多热源耦合加热块矿的烘干装置,包括烧结台车、点火保温炉及微波加热单元;所述点火保温炉布设于所述烧结台车料层前段的上方,其布设高度应满足所述点火保温炉的火焰外焰与所述烧结台车料层的上层物料实现接触加热的要求;所述微波加热单元布设于所述烧结台车料层后段的两侧。本发明首次提出利用钢铁厂欲淘汰的烧结机作为高炉精料用块矿烘干设备,通过多热源煤气燃料与微波的耦合加热烘干,既能够使旧装置发挥新功能,又提高了块矿烘干效率,满足在线
一种多热源供热水装置及多热源供热水控制方法.pdf
本发明公开了一种多热源供热水装置及多热源供热水控制方法,该多热源供热水装置通过在出热水管和回水管之间设置循环管路,从而能够在热水水箱的出热水口和回水口之间形成循环回路,该装置通过预先启动水泵,在水泵的驱动下,热水水箱的热水和各管路内的冷水能够在循环回路内循环从而实现热水和冷水的混合,并解决该装置启动时供热水管出水忽冷忽热的问题。并且,该多热源供热水装置能够根据温度检测机构检测到的热水水箱的出水温度控制第一管路切换机构、电加热器以及燃气热水器的工作状态,从而使不同温度的热水能够直接从供热水管流出或者经过不同
一种永磁耦合热源电采暖方法及装置.pdf
本发明公开一种永磁耦合热源电采暖方法及装置,包括永磁同步电机、永磁耦合器、热交换装置、蓄能水箱、散热器、电控设备;热交换装置包括金属发热体、循环水泵、循环水管线;金属发热体固定在热交换装置内部;永磁体镶嵌于绝缘阻热板中;永磁同步电机驱动永磁耦合器,永磁磁路耦合将电能转换为热能;蓄能水箱包括保温层,容量应大于等于散热器容水量;热交换装置与蓄能水箱相连接;金属发热体产生的热量给蓄能水箱水加热;蓄能水箱与散热器管线联通,加热后蓄能水箱水作为散热器热源;采用全新的磁路耦合原理,结合永磁耦合器与永磁电机的相关理论开
多热源耦合供热系统.pdf
本发明公开了一种多热源耦合供热系统,包括有热管平板式集热器、蒸汽压缩制热循环系统和燃气锅炉,热管平板式集热器包括有蛇形蒸发盘管、吸热板、热管、保温层、不锈钢板、水箱,蛇形蒸发盘管内有制冷剂;蒸汽压缩制热循环系统包括有压缩机、冷凝换热水箱、冷凝盘管、节流膨胀阀。本发明将普通热管平板式集热器吸收的未有效利用的热量被用于蒸汽压缩制热循环系统中,从而最大程度的充分利用太阳辐射能;在冷凝换热水箱设置三通阀,采暖用水与生活用水按季节要求切换使用,可以更合理的利用热水;在满足极端天气热水需求的同时考虑到全年平时热水需求