
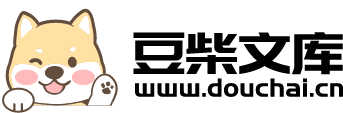
鞍山式磁铁矿选别流程.pdf
康平****ng
在线预览结束,喜欢就下载吧,查找使用更方便
相关资料
鞍山式磁铁矿选别流程.pdf
本发明提供了一种鞍山式磁铁矿选别流程,该鞍山式磁铁矿选别流程包括:矿浆经由弱磁选设备进行选别,获取弱磁精矿与弱磁尾矿;对所述弱磁精矿进行二次磁选,获取二次磁选精矿与二次磁选尾矿;所述弱磁尾矿通过强磁选设备进行选别,获取强磁精矿与强磁尾矿;所述二次磁选尾矿与所述强磁精矿合并通过反浮选进行选别,获取反浮选尾矿与反浮选精矿;所述反浮选精矿与所述二次磁选精矿合并作为精矿,所述强磁尾矿与所述反浮选尾矿合并作为尾矿、该鞍山式磁铁矿选别流程能够降低反浮选处理量,降低反浮选成本,降低尾矿品位,提高铁的回收率。
某贫磁铁矿短流程选别新工艺研究.pptx
汇报人:/目录0102贫磁铁矿的特点短流程选别工艺的必要性新工艺的研究背景和意义03破碎与磨矿磁选分离尾矿处理与再利用工艺流程的创新点04实验设备与方法实验结果与数据分析与传统工艺的比较新工艺的优势与局限性05新工艺在工业生产中的应用案例经济效益与社会效益分析对相关产业的影响与推动作用06技术创新与改进方向市场前景与发展趋势对未来工业发展的影响与贡献汇报人:
某贫磁铁矿短流程选别新工艺研究.docx
某贫磁铁矿短流程选别新工艺研究某贫磁铁矿短流程选别新工艺研究引言:贫磁铁矿是一种重要的铁矿石资源,其具有丰富的储量和广泛的分布。然而,由于其矿石赋存形式复杂、粒度偏细、铁品位低等特点,传统的选别工艺难以实现高效、经济的矿石提纯。因此,本文将对贫磁铁矿的选别工艺进行研究,旨在提出一种新的工艺方法,以期实现对贫磁铁矿的高效提矿。一、贫磁铁矿的特性与挑选难点贫磁铁矿主要由铁矿物和非铁矿物组成,其中非铁矿物包括硅酸盐、硅酸铁钠、黄铁矿等。铁矿物的磁化特性使得磁选成为贫磁铁矿选别的主要方法,然而,由于矿石的赋存形式
含碳酸铁贫磁铁矿选别工艺及设备参数优化.docx
含碳酸铁贫磁铁矿选别工艺及设备参数优化引言在矿床中,含碳酸铁贫磁铁矿是一种重要的矿物资源。其主要成分是Fe3O4和FeCO3,一般在铁矿石中占10%~15%。含碳酸铁贫磁铁矿的开采和加工不仅可以增加矿山开发的效益,还可以缓解铁矿石的资源短缺问题。因此,研究含碳酸铁贫磁铁矿的选别工艺及设备参数优化对于提高铁矿石资源利用率和经济效益有着重要的意义。一、匀矿筛分工艺优化匀矿筛分是矿物选别的最基本和最常用的方法。通过筛分,将原矿分成相对较大的块状矿物和相对较小的粒状矿物,以实现后续的处理和加工。在含碳酸铁贫磁铁矿
半坡锑矿石选别流程的研究.docx
半坡锑矿石选别流程的研究半坡锑矿石选别流程的研究摘要:本论文主要研究了半坡锑矿石的选别流程,对矿石的性质进行了分析,结合常用的选矿工艺和设备,提出了一种适用于半坡锑矿石的选别流程。研究结果表明,该流程能够有效提高半坡锑矿石的选别效果,并达到经济效益和环境可持续发展的要求。1.引言半坡锑矿石是一种含锑量较高的矿石资源,其中主要矿物为方铅矿。由于其性质的复杂性和难度较大,传统的选矿工艺和设备往往难以获得令人满意的选别效果。因此,研究半坡锑矿石的选别流程对于提高选矿效果和实现资源的高效利用具有重要意义。2.矿石