
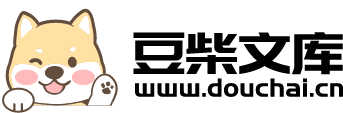
一种减少铸坯表面氧化铁皮的冶炼方法.pdf
书錦****by
在线预览结束,喜欢就下载吧,查找使用更方便
相关资料
一种减少铸坯表面氧化铁皮的冶炼方法.pdf
本发明公开一种减少铸坯表面氧化铁皮的冶炼方法,通过调整优化连铸二冷工艺,将连铸二次冷却强度比水量平均值由0.60L/Kg提高到0.70L/Kg,控制铸机上部至下部各区冷却水量比例波动幅度,提高浇铸方向上铸坯冷却均匀性,通过减少喷嘴堵塞实现良好的二冷喷水雾化效果,铸坯表面氧化铁皮厚度明显减少,平均厚度由1.45mm降低到0.65mm,提高了连铸钢水回收率,经济效益显著。
一种减少酸洗板表面黑线的铸坯冶炼方法.pdf
本发明特别涉及一种减少酸洗板表面黑线的铸坯冶炼方法,属于钢铁冶炼技术领域,方法包括:将铁水进行KR脱硫预处理,获得脱硫铁水;将所述脱硫铁水进行转炉冶炼,获得脱磷脱碳钢水;将所述脱碳钢水进行出钢,后进行RH精炼,获得精炼钢水;将所述精炼钢水进行连铸,获得铸坯,其中,所述连铸的保护渣的自由碳含量控制在1.5‑2.8%,所述保护渣的碳质颗粒的粒径控制在≥40μm,通过控制保护渣的自由碳含量和碳质颗粒的粒径,来防止卷渣进入钢坯形成黑线缺陷,进而实现减少酸洗板表面黑线。
一种去除铸坯氧化铁皮的装置及方法.pdf
本发明涉及一种去除铸坯氧化铁皮的装置及方法,属于连铸出坯标号设备技术领域。铸坯的一面为喷号面;通过在所述喷号面一侧对应设置可移动的喷号机;在所述喷号机面向喷号面的一侧设置喷号头和喷水装置;喷水装置和喷号头间隔设置;所述喷水装置上设有喷水管路,将所述喷水管路的一端与所述喷号面平行的喷水杆连通;并在所述喷水杆上连通多个面向所述喷号面的喷水头;在所述喷水管路上设置喷水阀,来解决因氧化铁皮导致炉号易脱落的技术问题。
一种铸坯表面氧化铁皮的清除设备及其使用方法.pdf
本发明涉及铸坯生产设备领域,具体来说是一种铸坯表面氧化铁皮的清除设备及其使用方法,所述清除设备包括多个设置在输送辊道上的清除装置,所述清除装置包括设置在输送辊道机构上的刮除装置,所述刮除装置包括支撑架,所述支撑架上设有刮除用的链条机构;所述链条机构包括多个单体链条,每个所述单体链条一端与支撑架相连接,另一端与处于输送辊道机构上的铸坯相接触。本发明公开了一种铸坯上氧化铁皮的清理装置,通过刮除装置和冲洗装置的配合使用,可以在不损伤铸坯质量的前提下,在铸坯生产的前端工序就能有效的清除铸坯表面的氧化铁皮。
一种减少铝脱氧高碳钢铸坯表面裂纹的方法.pdf
本发明涉及一种减少铝脱氧高碳钢铸坯表面裂纹的方法,其特征在于,在转炉熔炼、出钢脱氧、造渣、精炼、连铸各工序中分别对钢水中Als和N进行控制,抑制AlN的生成,从而降低高碳钢铸坯的表面裂纹,其操作步骤如下:1)降低钢水中的N含量;2)脱氧;3)顶渣中CaO/SiO2为1.5~2.5;4)精炼终点顶渣碱度CaO/SiO2为2.0~5.0;5)轧制前Als/N为2.32~6.68。与现有技术相比,本发明的有益效果是:1)通过对钢水中Als和N进行控制,抑制AlN的生成,从而有效降低高碳钢铸坯的表面裂纹,实现了即