
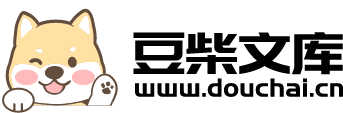
基于五轴超精密车削的表面微织构加工方法.pdf
小琛****82
在线预览结束,喜欢就下载吧,查找使用更方便
相关资料
基于五轴超精密车削的表面微织构加工方法.pdf
本发明公开了一种基于五轴超精密车削的表面微织构加工方法,将五轴联动数控加工的技术应用到了超精密车削上,可实现对加工工件表面进行确定性材料去除加工;与传统的通过激光加工、超声加工来制取表面微织构相比,该加工方法可以实现更加精准的对微织构制取进行控制,进而获得更好的加工精度与表面质量,可以满足表面微织构高精度、无干涉的确定性加工,并适用于各种复杂表面的微织构加工。
基于频率选择超构表面的单点多轴微角度精密测量.pdf
本发明公开了一种基于频率选择超构表面的单点多轴微角度精密测量方法,包括光源对准、超表面反射和反射光接收三个部分,光源对准的过程利用了超表面结构对可见光波段和近红外波段均存在吸收的特性,光频梳作为宽带光源,在一定程度上包含了超表面的特征吸收波段,通过与可见光经分束器混频之后作为光源输出,实现了可视化的激光光源对准过程;光源经准直镜准直后照射到超表面的结构上,由于结构之间存在差异性,对光频梳的吸收也会有所不同,在近红外相机成像的结果中体现为结构的亮度变化,超表面安装在待测机构表面,电动操纵转台用于精确的控制待
表面沟槽微织构刀具高速微车削试验研究.docx
表面沟槽微织构刀具高速微车削试验研究摘要:本文以表面沟槽微织构刀具为研究对象,采用高速微车削技术进行试验研究。通过测量刀具在不同微织构条件下的切削力、表面粗糙度和工件表面形貌等参数,分析了微织构刀具对高速微车削加工的影响。研究结果表明,在适当的微织构条件下,可以有效降低切削力和表面粗糙度,并且能够在一定程度上改善工件表面形貌。关键词:表面沟槽微织构刀具;高速微车削;切削力;表面粗糙度;工件表面形貌引言:近年来,随着制造技术的不断进步,高速微车削技术已经成为先进制造领域的关键技术之一。而表面沟槽微织构技术则
一种电解加工表面微织构的方法.pdf
本申请公开了一种电解加工表面微织构的方法,其特征在于,所述方法包含工具阴极、电解加工电源、电解液、激光光束发生器;所述工具阴极包含光导电层和透明导电层。该方法利用光导电层和透明导电层组成的工具阴极实现表面微织构的电解加工,具有表面微织构轮廓实时可控,无需涂胶、光刻、曝光等复杂过程,针对不同表面微织构加工无需更换工具阴极,可对任意曲面工件表面加工微织构等优点。
刀具表面微织构激光加工方法研究与分析.docx
刀具表面微织构激光加工方法研究与分析刀具表面的微织构在现代制造业中起着重要的作用,它可以改善刀具的摩擦性能、降低摩擦阻力、延长刀具使用寿命等。而激光加工作为一种非接触加工技术,具有高精度、高效率、无变形等优点,近年来被广泛应用于刀具表面微织构的加工中。本文将对刀具表面微织构激光加工方法进行研究与分析。一、刀具表面微织构的意义1.提高刀具的摩擦性能:刀具表面微织构可以增加刀具与工件之间的接触面积,提高摩擦系数,从而减少切削力和摩擦阻力。2.延长刀具的使用寿命:刀具表面微织构可以减少切削温度,提高切削润滑效果