
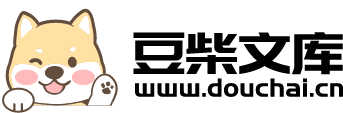
超声冲击对P355NL1钢焊接接头超高周疲劳性能的影响.doc
猫巷****婉慧
在线预览结束,喜欢就下载吧,查找使用更方便
相关资料
超声冲击对P355NL1钢焊接接头超高周疲劳性能的影响.doc
超声冲击对P355NL1钢焊接接头超高周疲劳性能的影响本文通过超声疲劳实验、模拟应力集中、探测残余应力及焊接接头表面晶粒细化来探究超声冲击对P355NL1钢焊接接头超高周疲劳性能的影响。试验将试样分成5组,分别是圆柱状母材试样、板状母材试样、圆柱状焊接接头试样、板状焊接接头试样和超声冲击态试样。五组试样进行超声疲劳试验,获得五组疲劳试验数据和S-N曲线,对比五组试验数据,得到超声冲击对P355NL1钢焊接接头的超高周疲劳性能影响。利用扫描电镜(SEM)观察五组试样的疲劳失效断口形貌,探究其疲劳失效模式。通
超声冲击对P355NL1钢焊接接头超高周疲劳性能的影响.doc
超声冲击对P355NL1钢焊接接头超高周疲劳性能的影响本文通过超声疲劳实验、模拟应力集中、探测残余应力及焊接接头表面晶粒细化来探究超声冲击对P355NL1钢焊接接头超高周疲劳性能的影响。试验将试样分成5组,分别是圆柱状母材试样、板状母材试样、圆柱状焊接接头试样、板状焊接接头试样和超声冲击态试样。五组试样进行超声疲劳试验,获得五组疲劳试验数据和S-N曲线,对比五组试验数据,得到超声冲击对P355NL1钢焊接接头的超高周疲劳性能影响。利用扫描电镜(SEM)观察五组试样的疲劳失效断口形貌,探究其疲劳失效模式。通
超声冲击对含缺陷焊接接头疲劳性能的影响.pptx
超声冲击对含缺陷焊接接头疲劳性能的影响目录添加章节标题引言背景介绍研究目的和意义研究内容和方法超声冲击技术原理超声冲击技术概述超声冲击设备及工艺参数超声冲击对材料表面的影响含缺陷焊接接头疲劳性能研究焊接接头疲劳性能概述缺陷类型及对疲劳性能的影响疲劳性能测试方法及实验结果分析超声冲击对含缺陷焊接接头疲劳性能的影响研究实验设计及材料准备超声冲击处理对焊接接头疲劳性能的影响结果分析与讨论结论与展望研究成果总结未来研究方向与展望对实际应用的建议与价值评估THANKYOU
超声冲击态焊接接头疲劳性能分析.docx
超声冲击态焊接接头疲劳性能分析超声冲击态焊接接头疲劳性能分析摘要:超声冲击态焊接是一种高效、环保、低温焊接技术,具有广泛的应用前景。本文通过文献研究和实验分析,探讨了超声冲击态焊接接头的疲劳性能。研究表明,超声冲击态焊接接头在疲劳载荷作用下表现出良好的疲劳性能,但也存在一定的局限性。通过对接头的微观组织和断口形貌的分析,可以进一步优化超声冲击态焊接工艺,提高接头的疲劳寿命。关键词:超声冲击态焊接,接头,疲劳性能,微观组织引言:超声冲击态焊接是一种通过超声波的辐射热和冲击力来实现固态焊接的新技术。由于其低温
超声冲击对SMA490BW耐候钢焊接接头疲劳性能的影响研究.doc
超声冲击对SMA490BW耐候钢焊接接头疲劳性能的影响研究SMA490BW作为高强钢已被用于列车转向的构架上,转向架焊接构架焊趾处的应力集中和残余应力等不利因素导致转向架焊接接头处首先出现疲劳裂纹,随着这些裂纹不断的扩展最终导致焊接构架的失效,大大降低了列车转向架的疲劳寿命,故焊趾是焊接件承载能力的薄弱环节。超声冲击处理是一种通过细化金属表层晶粒,增加表面硬化程度,减少材料中存在的缺陷以及在表层引入有益的残余压应力来提高金属结构件性能的表面强化技术。该技术以超声波为动力源,利用其高频、高能的特点冲击金属表