
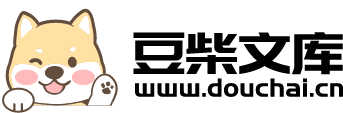
一种复合材料管连接结构及其制备方法.pdf
是来****文章
亲,该文档总共11页,到这已经超出免费预览范围,如果喜欢就直接下载吧~
相关资料
一种复合材料管连接结构及其制备方法.pdf
本发明公开了一种复合材料管连接结构,包括金属内插管,金属内插管插接在复合材料管中,两者之间设置有粘结胶层,复合材料管上开设有供连接螺钉穿过的孔,连接螺钉的杆体上环套有工字型的纤维编织管,且且上、下端面分别卡接在复合材料管的外壁和内壁上,纤维编织管的上端面与连接螺钉之间环套有仿生补强环;该结构的制备方法为:依次制备复合材料管连接结构中的各部件,然后组装连接并进行固化、清理打磨和加工。本发明设置纤维编织管和仿生补强环对复合材料管开孔处进行补强,实现了对复合材料管内壁和外壁的全面整体补强作用;本发明基于应力分布
一种用于高压管件连接的连接结构及其连接方法.pdf
本发明涉及高压管件技术领域,具体为一种用于高压管件连接的连接结构,包括第一连接结构及第二连接结构;第一连接结构包括主连接盘、转动盘、连接管道、延伸杆及螺纹套环,连接管道另一端表面开设外螺纹结构,连接管道开设外螺纹孔结构一端横向开设若干个通槽,第一连接结构包括主连接盘及第二连接结构包括主连接盘上分别设置第一连接盘和第二连接盘,第一连接盘内侧面设置若干个螺纹杆,第二连接盘上开设若干个通孔,螺纹杆贯穿通孔并通过螺帽固定。本发明能够代替传统的焊接连接方式将两根高压管道进行连接,不需要具备一定的焊接技术要求就能够实
一种连接管结构及其制备方法.pdf
本发明公开了一种连接管结构及其制备方法,包括吸气外管、铁质吸气内管和用于与壳体进行电阻焊的铁质连接底座,其特征在于:所述的吸气外管为铁基材管,其一端与铁质吸气内管连通,另一端具有与外界进行焊接连接的焊接区域,吸气外管至少焊接区域的外表面具有由铜铁扩散工艺形成的至少包括一层铜‑铁相互扩散层的表面处理层。本发明对储液器或消音器的连接管进行了改善,采用铁为基材,价格较低,通过铜铁扩散工艺使其表面形成表面处理层,可抗过炉焊的高温,基本杜绝了接口处的铜管发生断裂的风险,制备时可以将铁质吸气内管、吸气外管和铁质连接底
一种口腔连接结构及其制备方法.pdf
本发明公开了一种口腔连接结构,包括基台结构,所述基台结构包括连接体与基台体,所述基台体安装在连接体的上端位置,且基台体的顶部设置有密封组件,所述连接体包括螺纹套与螺纹筒,螺纹筒的顶端安装有啮合段,螺纹套的外部设置有螺纹段,且螺纹套的底部连接有啮合段,螺纹套的底端设置有锥头,所述基台体包括羟基磷灰石体一和羟基磷灰石体二,羟基磷灰石体一设置在羟基磷灰石体二的下端;本发明实现了口腔连接结构的组装,实现了现场快速组装的需求,同时配备有生物活性物质,以模拟生物信号,来刺激细胞粘附、增殖、分化等的行为,有利于口腔连接
柔性材料连接结构及其制备方法.pdf
本申请公开了柔性材料连接结构及其制备方法,柔性材料连接结构包括一体成型的第一柔性材料、第二柔性材料和橡胶连接部,第一柔性材料和第二柔性材料均分为连接段和延伸段;第一柔性材料的连接段和第二柔性材料的连接段均设有若干垂直通孔,垂直通孔用于流入熔化的橡胶后固化成型,以实现与橡胶连接部竖直方向的固定连接;沿第一柔性材料的连接段、第二柔性材料的连接段的长度方向设有若干楔形结构,以实现与橡胶连接部水平方向的固定连接;或第一柔性材料的连接段和第二柔性材料的连接段均为凸出块状结构。本申请提供的柔性材料连接结构可实现不借助