
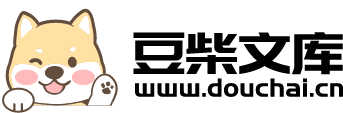
冲裁模试冲时出现的问题及调整方法.doc
玄静****写意
在线预览结束,喜欢就下载吧,查找使用更方便
相关资料
冲裁模试冲时出现的问题及调整方法.doc
冲裁模试冲时出现的问题及调整方法存在问题产生原因调整方法冲裁件的形状和尺寸不正确凸模与凹模的形状及尺寸不正确先将凸模和凹模的形状及尺寸修准,然后调整冲模的合理间隙。冲裁件的剪切断面的光亮带太宽,甚至出现双光亮带及毛刺冲裁间隙太小适当放大冲裁间隙,放大的办法是用油石仔细修磨凹模及凸模刃口冲裁件的剪切断面的圆角太大,甚至出现拉长的毛刺冲裁间隙太大适当减小冲裁间隙,减小的办法是重新更换加大了尺寸的凸模或将凹模加热至800℃左右,用淬硬压柱压之刃口后再将其进行正常化处理,以消除热压后材料内部产生的组织应力和热应力
冲裁模试冲时出现的问题及调整方法.doc
冲裁模试冲时出现的问题及调整方法存在问题产生原因调整方法冲裁件的形状和尺寸不正确凸模与凹模的形状及尺寸不正确先将凸模和凹模的形状及尺寸修准,然后调整冲模的合理间隙。冲裁件的剪切断面的光亮带太宽,甚至出现双光亮带及毛刺冲裁间隙太小适当放大冲裁间隙,放大的办法是用油石仔细修磨凹模及凸模刃口冲裁件的剪切断面的圆角太大,甚至出现拉长的毛刺冲裁间隙太大适当减小冲裁间隙,减小的办法是重新更换加大了尺寸的凸模或将凹模加热至800℃左右,用淬硬压柱压之刃口后再将其进行正常化处理,以消除热压后材料内部产生的组织应力和热应力
冲裁及冲裁模设计.pptx
1第2章冲裁34567891011121314冲裁区应力、变形和冲裁件正常的断面状况a)冲孔件b)落料件1617181920212223在冲压实际生产中,主要根据冲裁件断面质量和模具寿命这二个因素综合考虑,给间隙规定一个范围值。考虑到在生产过程中的磨损使间隙变大,故设计与制造新模具时应采用最小合理间隙Zmin252627282930313233343536373839404142434445462.4.1冲裁力的计算(平刃)4849505152排样:54一个步距内的材料利用率一张板料(或带料、条料)上总的
冲裁工艺及冲裁模设计.docx
编号:时间:2021年x月x日书山有路勤为径学海无涯苦作舟页码:第二章冲裁工艺及冲裁模设计一、填空题1.冲裁既可以直接冲制________又可以为其他__________制备毛坯。2.一般来说冲裁工艺主要是指_____和_____工序。冲裁变形过程大致可分为_______、________、________三个阶段。冲裁件的切断面由______、______、_______、_____四个部分组成。光亮带是紧挨圆角带并与________的光亮部分它是在
冲裁工艺及冲裁模设计.doc
第二章冲裁工艺及冲裁模设计一、填空题1.冲裁既可以直接冲制________,又可以为其他__________制备毛坯。2.一般来说,冲裁工艺主要是指_____和_____工序。冲裁变形过程大致可分为_______、________、________三个阶段。冲裁件的切断面由______、______、_______、_____四个部分组成。光亮带是紧挨圆角带并与________的光亮部分,它是在塑性变形过程中凸模与凹模挤压切入材料,使其受到_______和________的作用而形成的。冲裁毛刺是在刃口附